Pimp up your fabric
Open-width tumble washing and wet treatments
Biancalani AQUARIA®, the innovative open-width continuous tumble washing range for any kind of textile wet treatment. The one and only washing system which concurrently offers extended and adjustable dwell times together with effective mechanical action, in a safe open-width process.
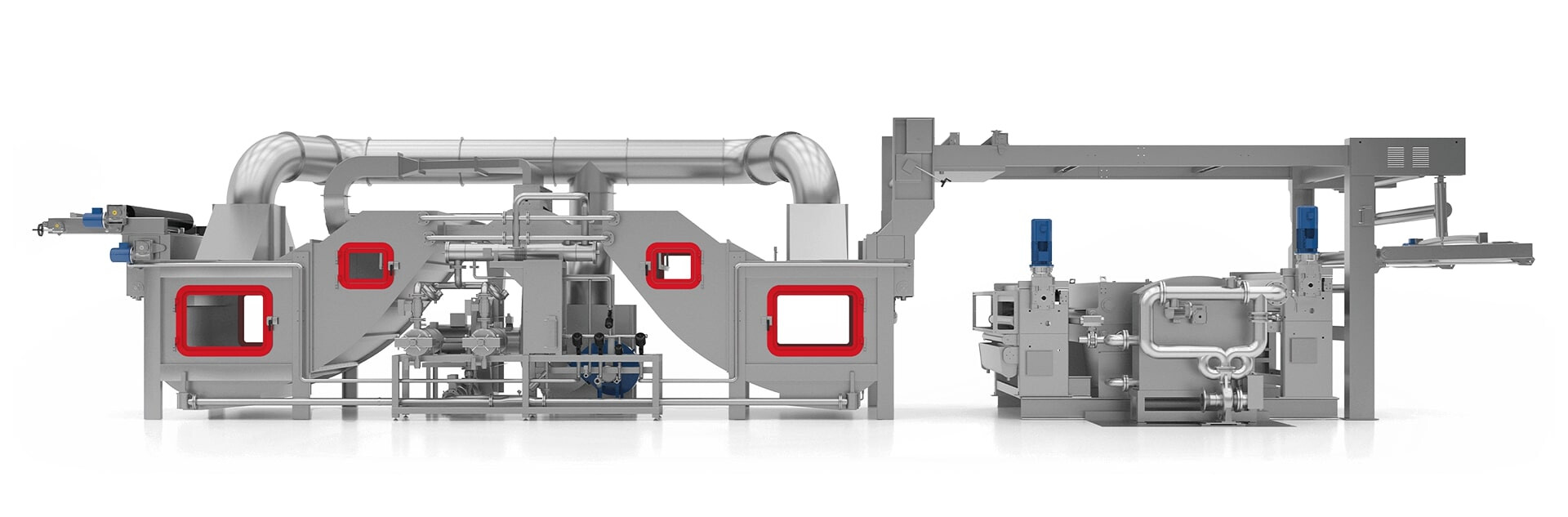
Up to 80 metres per minute
Up to 600 metres per minute
20-500 metres of fabric accumulation
Starting from just 500 litres
APPLICATIONS AND TREATMENTS
Eco-bleaching
Full or partial bleaching of any woven or knitted fabric in cotton/cellulosic fibres before dyeing or printing, using zero caustic, zero liquid peroxide, zero chlorine, and with zero water discharge, for a relaxed 100% defect-free and green process which also improves the final hand and feel of the fabric.
Washing after dyeing and reactive printing
Efficient washing to remove the excess ink/thickener and ensure high levels of colour fastness after digital or conventional printing or after any dyeing process, with low water consumption in a relaxed process which is 100% safe, free from any wrinkle or crease mark, and contributes to improve the final hand and feel of fabric.
Organic scouring of synthetic fabric
Removal of oils from woven or knitted fabric in polyester and other synthetic fibres, with a safe, relaxed, and 100% green process that uses a low amount of water and no solvents, and improves the final hand and feel of fabric.
Denim fabric: indigo shade reduction, washing, fixing
Partial bleaching of indigo-dyed denim for reduction up to 50% of original shade, quick wash to remove dust and unfixed indigo, or with chemical fixation to keep colour dark with better crocking, innovative soft-hand flat finish and shade enhancement. With zero caustic, zero liquid peroxide, zero chlorine, low water consumption, in a safe and relaxed process contributing to effective width reduction and warp shrinkage and to the final hand and feel of fabric.
Scouring and light milling of woollen fabric
Efficient removal of grease and dirt, and light milling for any woollen and blended fabric, woven or knitted, with low water consumption in a completely safe, relaxed, and 100% green process.
Relaxed mercerization or caustification for cotton and denim fabric
Increased dimensional stability, with warp shrinkage and width reduction, and a new and unique hand and touch which is completely different from traditional mercerization, with low water consumption in a relaxed and 100% defect-free process.
Soda treatment of polyester (weight reduction) and silk (opaline effect)
Uniquely soft and silky hand and touch for polyester, and opaline effect with frosted look for silk fabric, woven or knitted, with low water consumption in a relaxed and 100% defect-free process.
Full preparation of lyocell
Implementing the recommended preparation procedure for woven and knitted lyocell and blends, which includes mechanical fibrillation and efficient enzyme washing for anti-pilling effect and special hand touch and look, in a relaxed process with low water usage, 100% safe and free from any wrinkle or crease mark.
Fibrillation of cupro, modal, and cellulosic fibers
Preparation treatment for any cupro, modal, and lyocell fabric, woven or knitted, for a special hand feel and touch or in preparation to anti-pilling treatments, in a 100% safe and defect free relaxed process with low water consumption.
Enzyme washing and biopolishing
Bio-polishing, anti-pilling and special hand touch, washed-out colour (délavé), aged look, peach skin effect on any woven or knitted cotton/cellulosic and blended fabrics, using a 100% green process with zero water discharge on undyed fabric, completely safe and free from any crease mark or wrinkle.
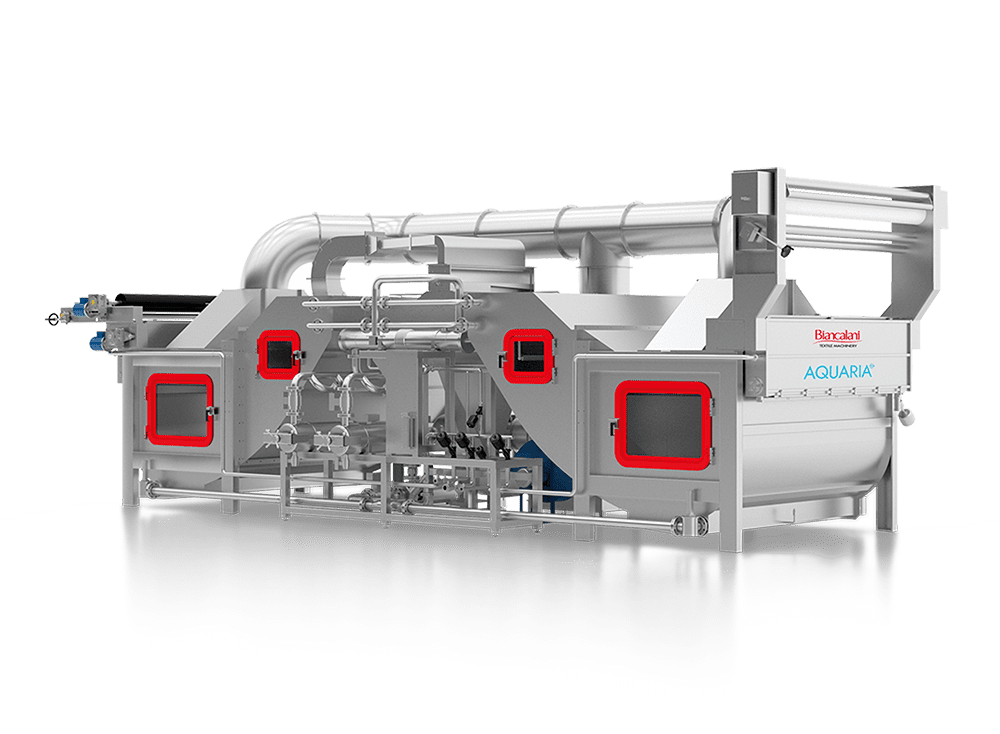
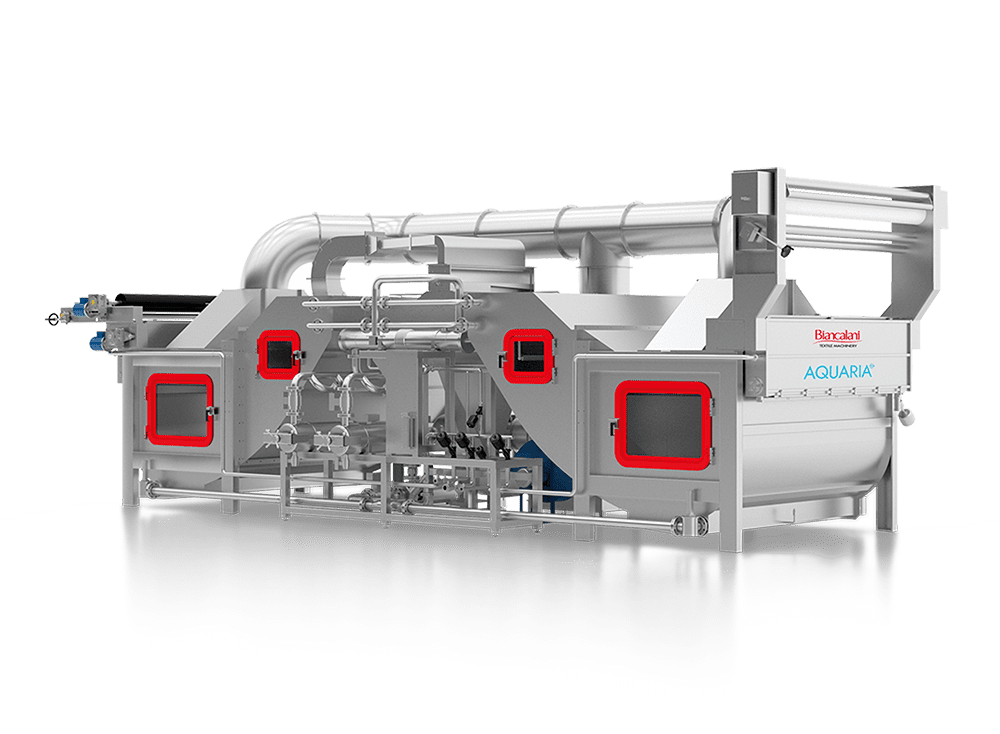
Eco-bleaching
Full or partial bleaching of any woven or knitted fabric in cotton/cellulosic fibres before dyeing or printing, using zero caustic, zero liquid peroxide, zero chlorine, and with zero water discharge, for a relaxed 100% defect-free and green process which also improves the final hand and feel of the fabric.
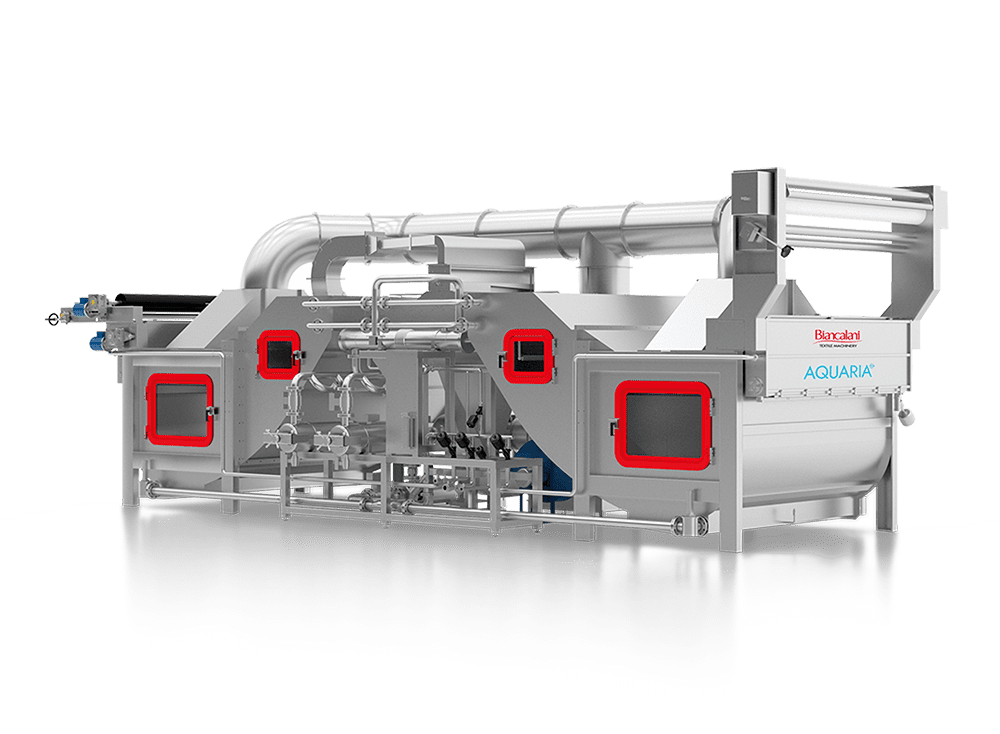
Washing after dyeing and reactive printing
Efficient washing to remove the excess ink/thickener and ensure high levels of colour fastness after digital or conventional printing or after any dyeing process, with low water consumption in a relaxed process which is 100% safe, free from any wrinkle or crease mark, and contributes to improve the final hand and feel of fabric.
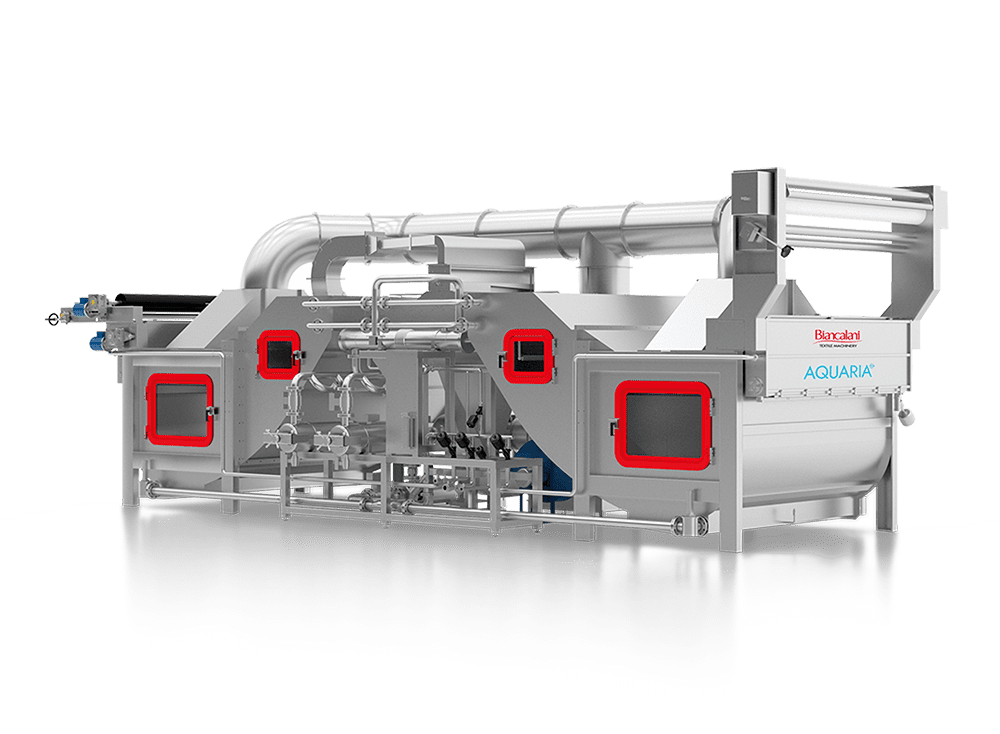
Organic scouring of synthetic fabric
Removal of oils from woven or knitted fabric in polyester and other synthetic fibres, with a safe, relaxed, and 100% green process that uses a low amount of water and no solvents, and improves the final hand and feel of fabric.
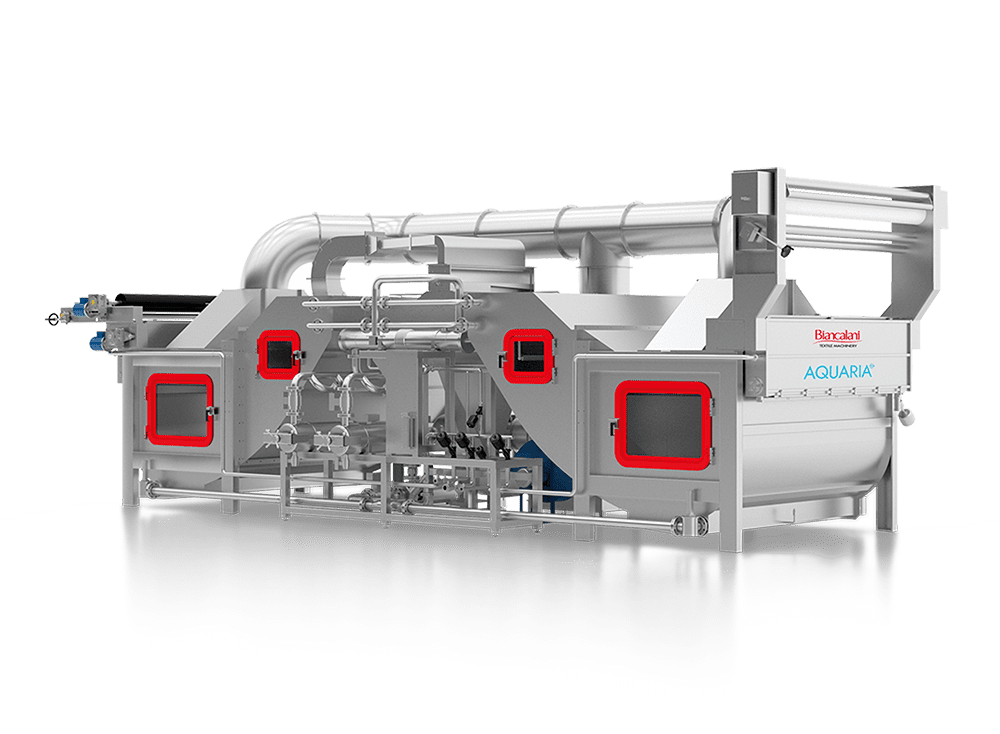
Denim fabric: indigo shade reduction, washing, fixing
Partial bleaching of indigo-dyed denim for reduction up to 50% of original shade, quick wash to remove dust and unfixed indigo, or with chemical fixation to keep colour dark with better crocking, innovative soft-hand flat finish and shade enhancement. With zero caustic, zero liquid peroxide, zero chlorine, low water consumption, in a safe and relaxed process contributing to effective width reduction and warp shrinkage and to the final hand and feel of fabric.
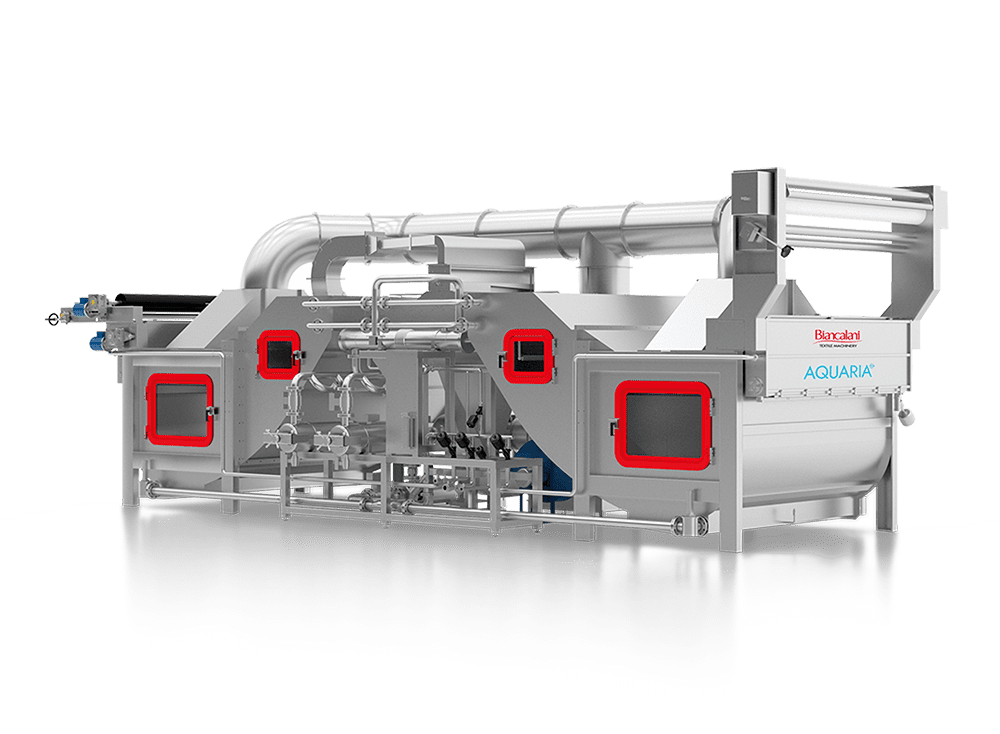
Scouring and light milling of woollen fabric
Efficient removal of grease and dirt, and light milling for any woollen and blended fabric, woven or knitted, with low water consumption in a completely safe, relaxed, and 100% green process.
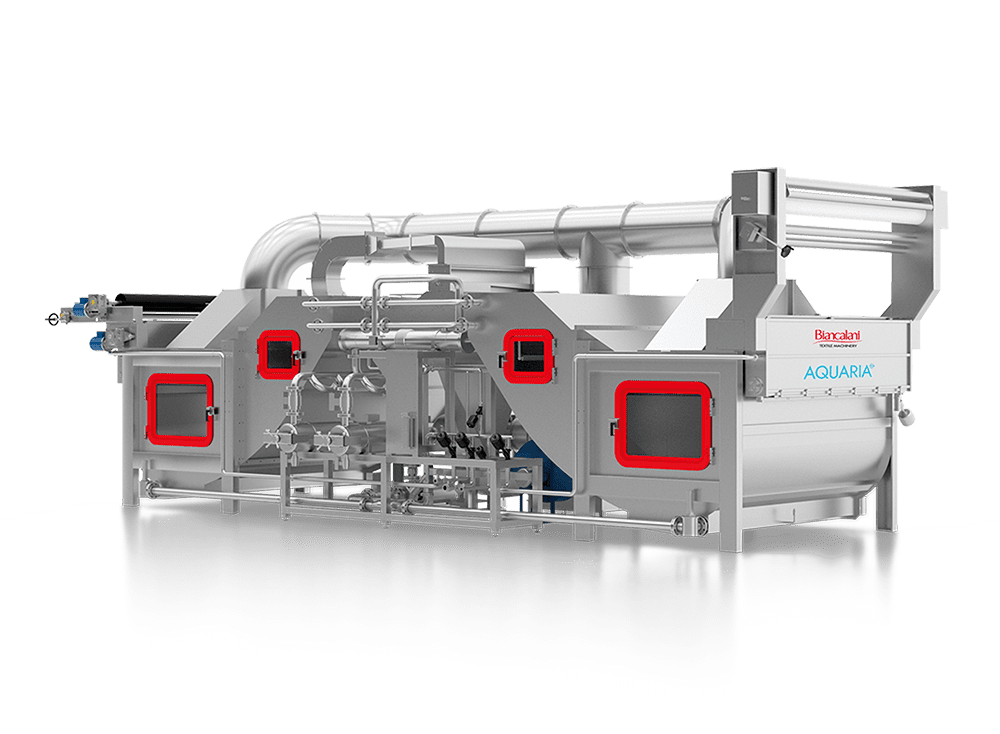
Relaxed mercerization or caustification for cotton and denim fabric
Increased dimensional stability, with warp shrinkage and width reduction, and a new and unique hand and touch which is completely different from traditional mercerization, with low water consumption in a relaxed and 100% defect-free process.
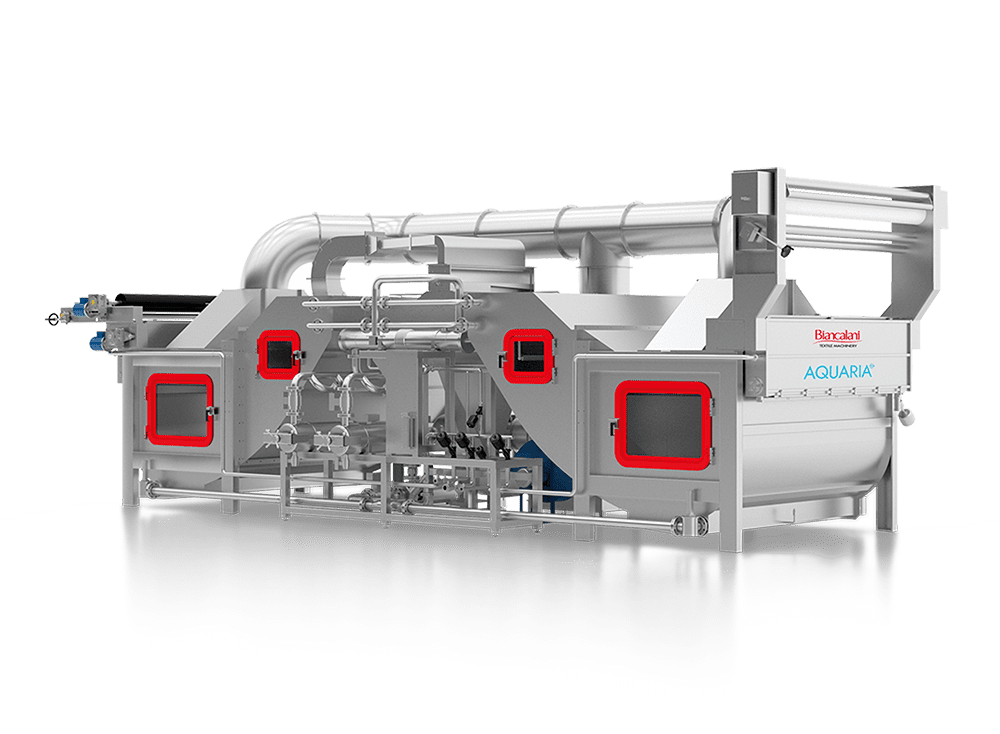
Soda treatment of polyester (weight reduction) and silk (opaline effect)
Uniquely soft and silky hand and touch for polyester, and opaline effect with frosted look for silk fabric, woven or knitted, with low water consumption in a relaxed and 100% defect-free process.
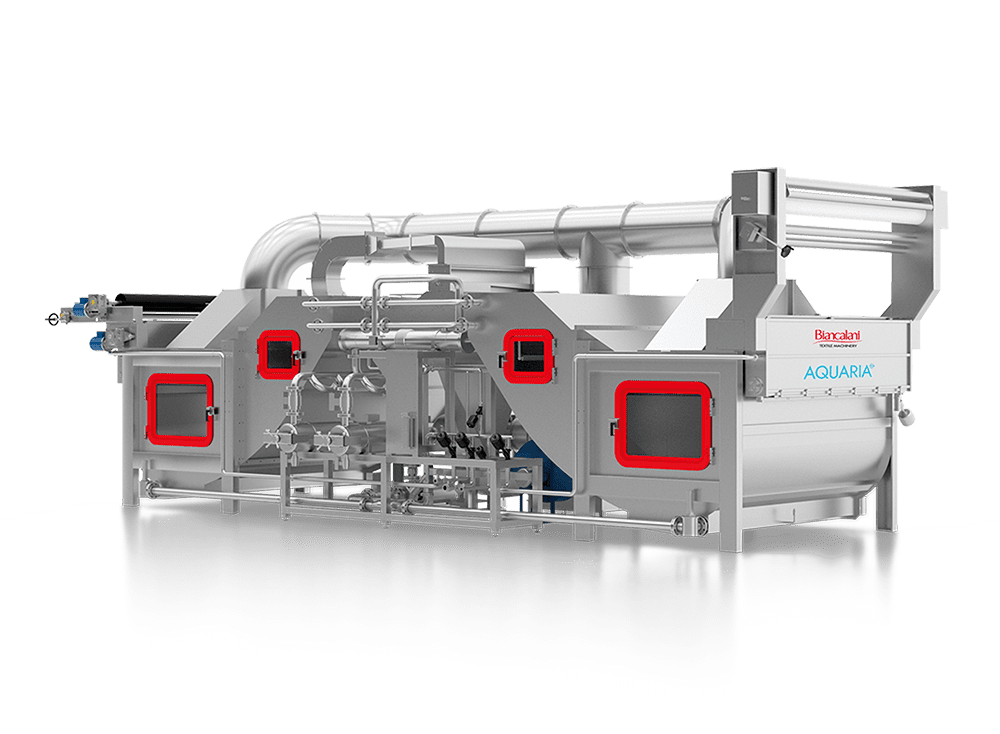
Full preparation of lyocell
Implementing the recommended preparation procedure for woven and knitted lyocell and blends, which includes mechanical fibrillation and efficient enzyme washing for anti-pilling effect and special hand touch and look, in a relaxed process with low water usage, 100% safe and free from any wrinkle or crease mark.
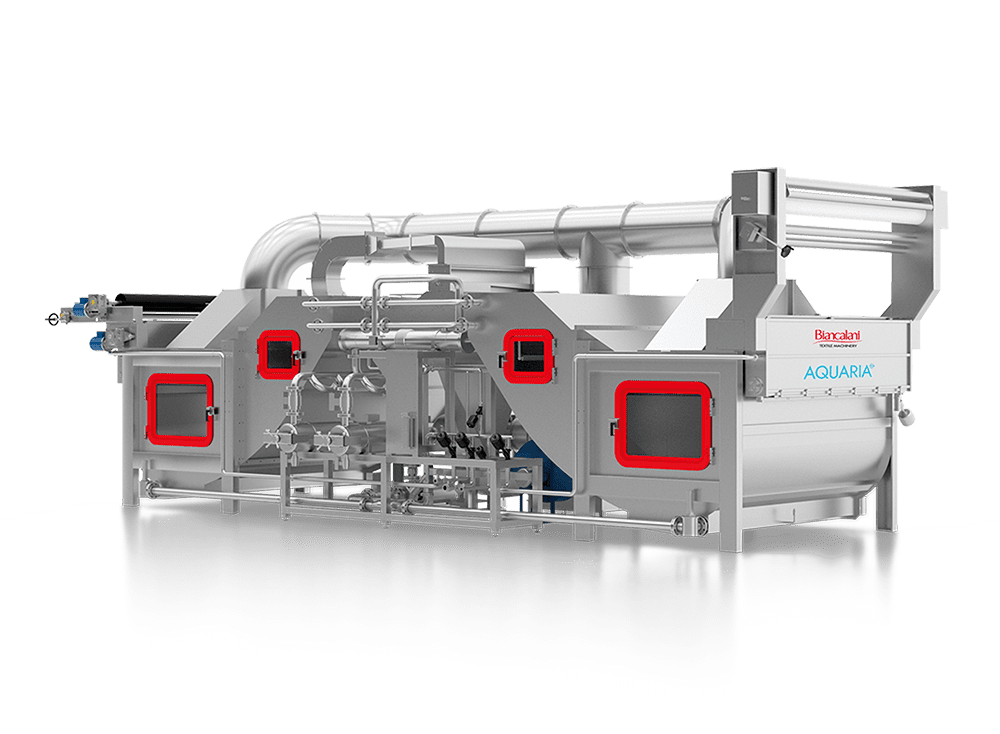
Fibrillation of cupro, modal, and cellulosic fibers
Preparation treatment for any cupro, modal, and lyocell fabric, woven or knitted, for a special hand feel and touch or in preparation to anti-pilling treatments, in a 100% safe and defect free relaxed process with low water consumption.
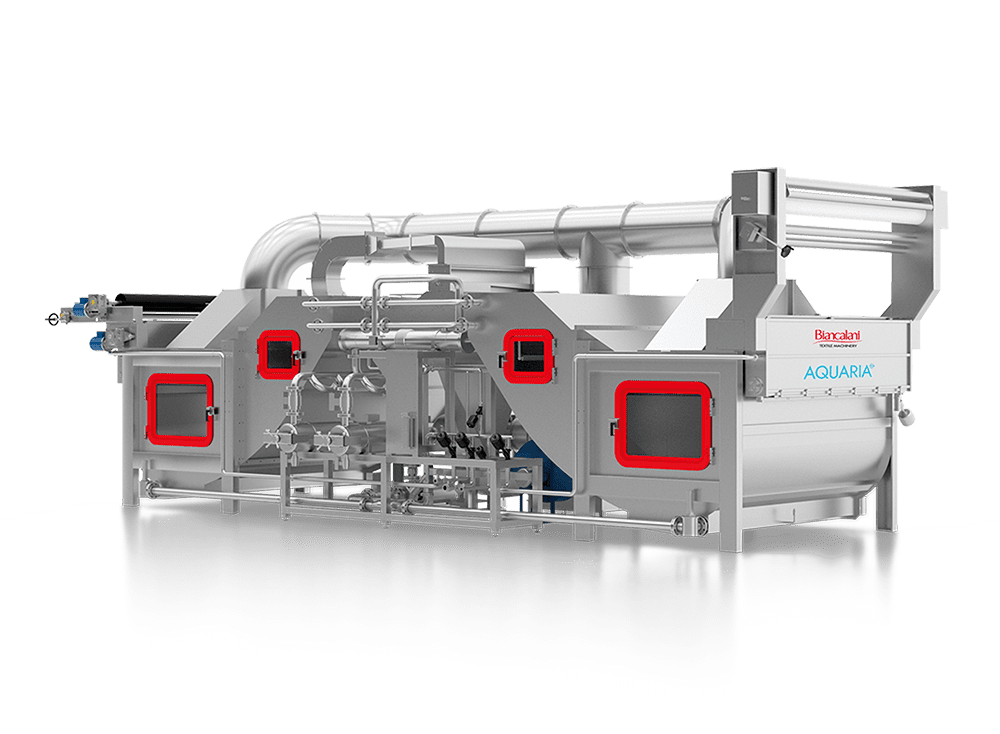
Enzyme washing and biopolishing
Bio-polishing, anti-pilling and special hand touch, washed-out colour (délavé), aged look, peach skin effect on any woven or knitted cotton/cellulosic and blended fabrics, using a 100% green process with zero water discharge on undyed fabric, completely safe and free from any crease mark or wrinkle.
Example configurations and lines

BASIC MULTI-PURPOSE WASHING

WASHING AND FINISHING AFTER PRINTING/DYEING

ZERO-WATER ECO-BLEACH / POLYESTER WEIGHT REDUCTION / RELAXED MERCERIZATION

LARGE CAPACITY MULTI-PURPOSE WASHING
Main AQUARIA® washing module

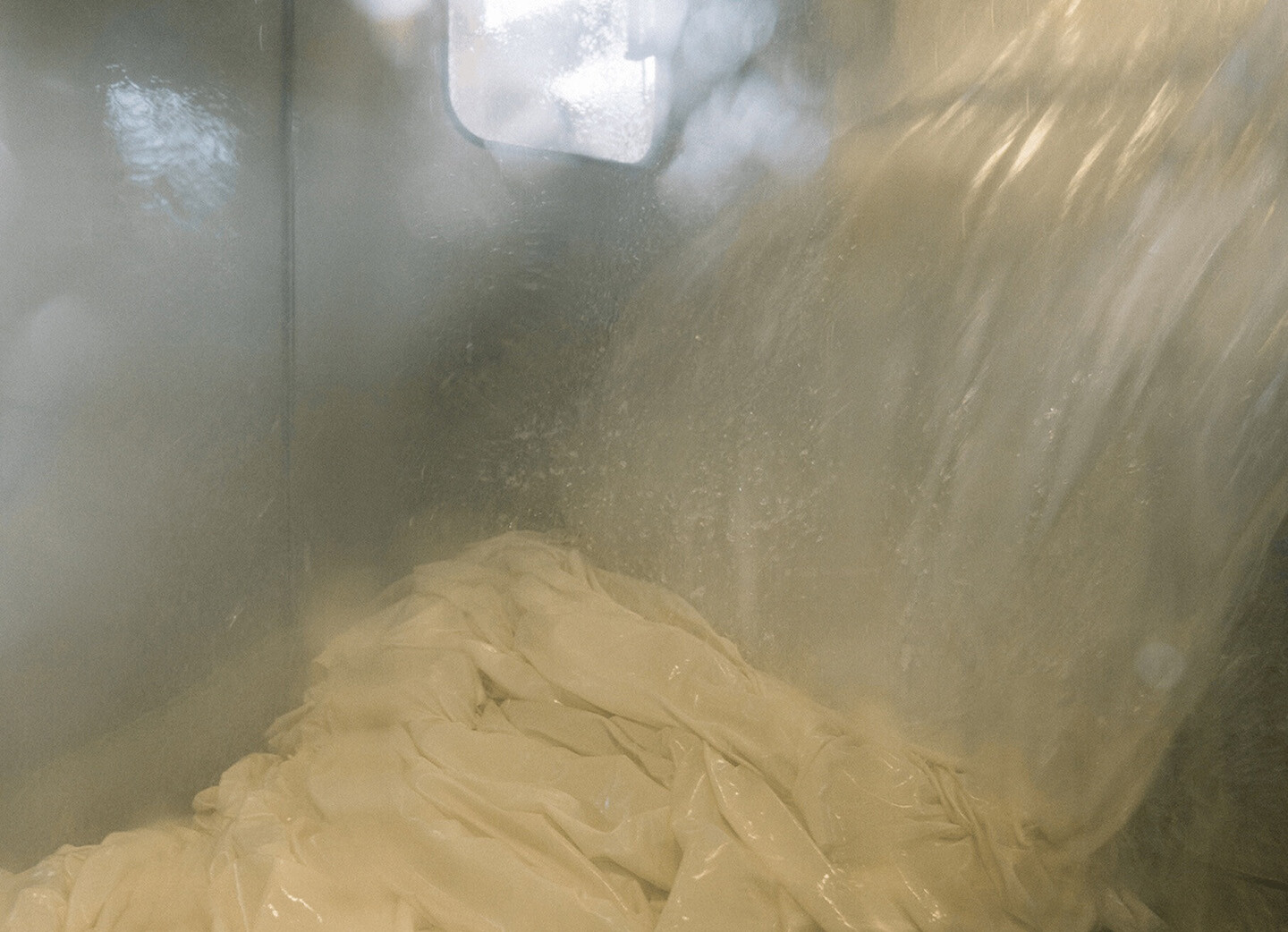
The most intensive washing ever
The innovative open-width continuous AQUARIA® washing system, patented by Biancalani, is based on the AIRO® concept of moving the fabric solely by air, and applying real mechanical action to the fabric while washing it.
With the experience and expertise of Biancalani in the air transportation of fabric, which guarantees safe and defect-free treatment, AQUARIA® brings new solutions to the finishing sector, and new sustainable and efficient ways to perform any traditional washing treatment.
Here’s how it works
AQUARIA® is made up of two large accumulation chambers, connected by a pneumatic ejector (the treatment channel), with impact grills at its ends. Fabric moves at high speed inside the channel, impacts against the grids, and accumulates inside the chambers, where it can lay immersed in the process bath. A continuous nebulisation of the process bath through sprayers placed at each side of treatment channel keeps the fabric permanently and uniformly wet.
Efficient washing with variable water level
The power of air pushes the process bath inside the treatment channel and through the fabric, forcing it to penetrate deeply into the fibres. At the exit of the channel, the energetic impact against the grill quickly releases most of the water, for a continuous and efficient washing action.
This allows increasing the productivity of the washing line, while maintaining liquor ratio values as low as 1:6.
Extended adjustable dwell time and mechanical action
AQUARIA® is the only machine capable of processing open-width fabric at high speed, in complete safety, for a powerful mechanical action. At the same time, it offers very long dwell times, freely adjustable by varying the amount of fabric accumulation inside the machine.
This, together with the high exchange between air and water over the whole surface of the open width fabric, makes it ideal for continuous open-width enzyme treatments, and provides a fully sustainable approach to bleaching (AQUARIA® caustic-free eco-bleaching with zero-water discharge), scouring, and fashion effects.
Well equipped for every need
High pressure and flow recirculation pumps, independent sprayers at the entrance of treatment channel inside the two accumulation chambers, indirect heating of the process bath for temperatures up to 98°C, water filtering devices, dosing systems for chemical products with controlled bath renewal and automatic level management: AQUARIA® includes everything for an automatized, efficient, and homogeneous wash.
Perfect washing is a piece of cake!
A centralized touch screen, with auxiliary controls distributed over the whole line, and a simple user interface, provide complete control and storage into recipes of all the working parameters, as well as real-time monitoring of process data and utility consumptions for each process.
All the modules in the washing line are seamlessly interconnected and can be dynamically configured to offer a complete and versatile solution for any kind of wet processing.
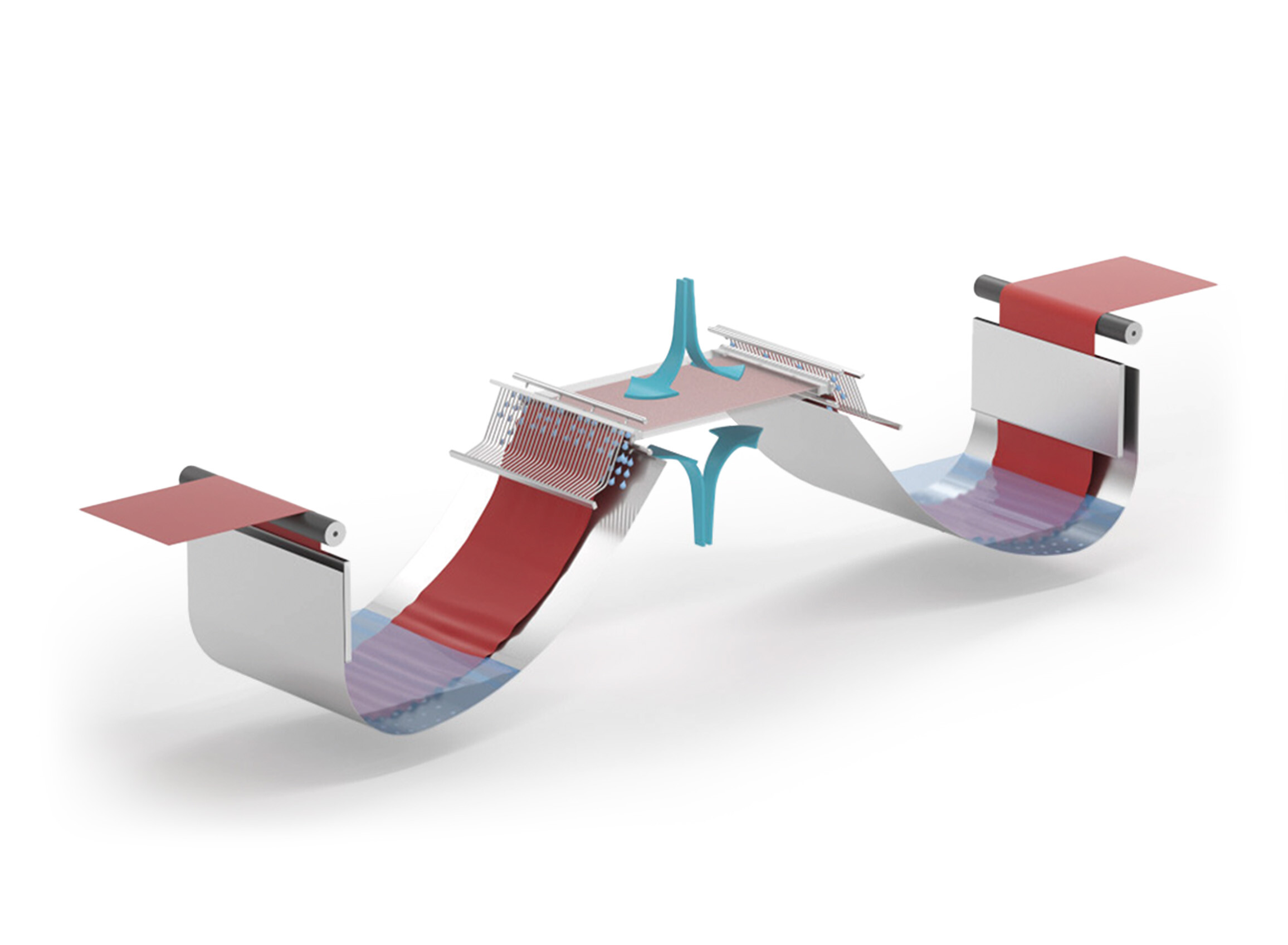
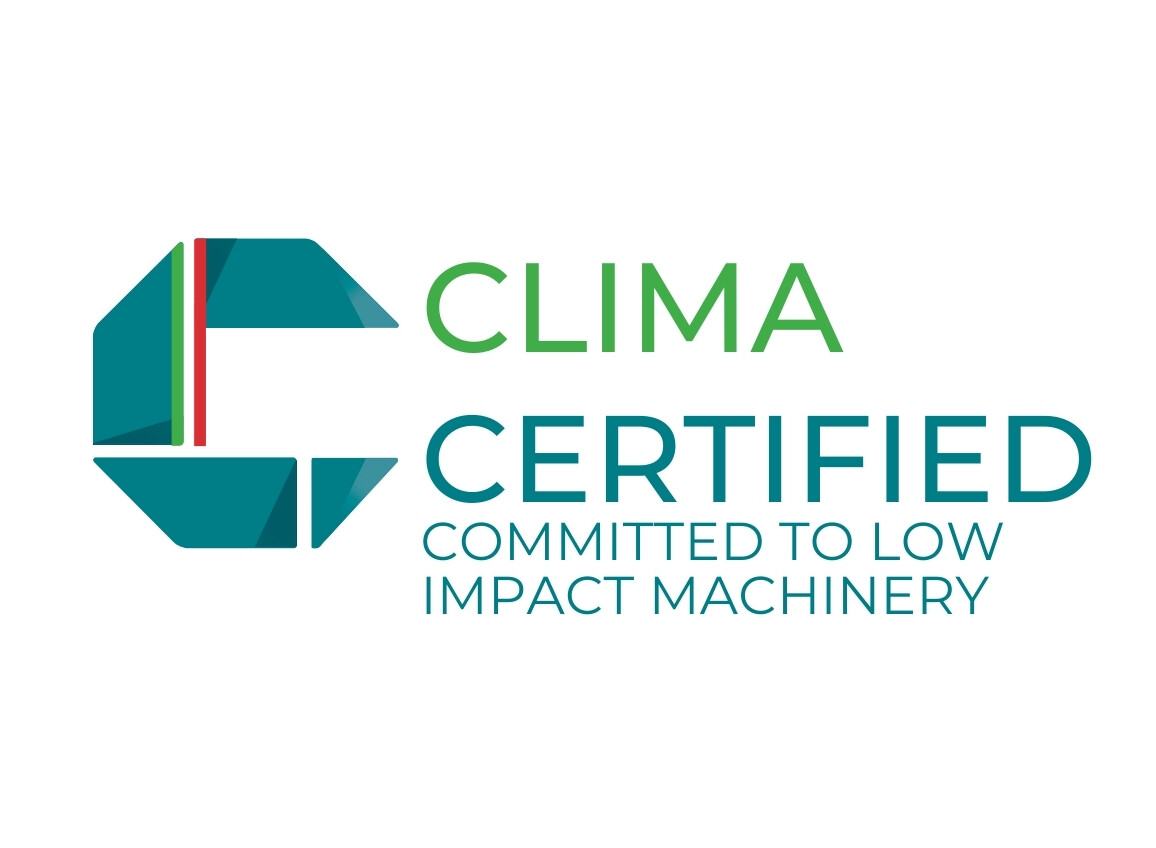
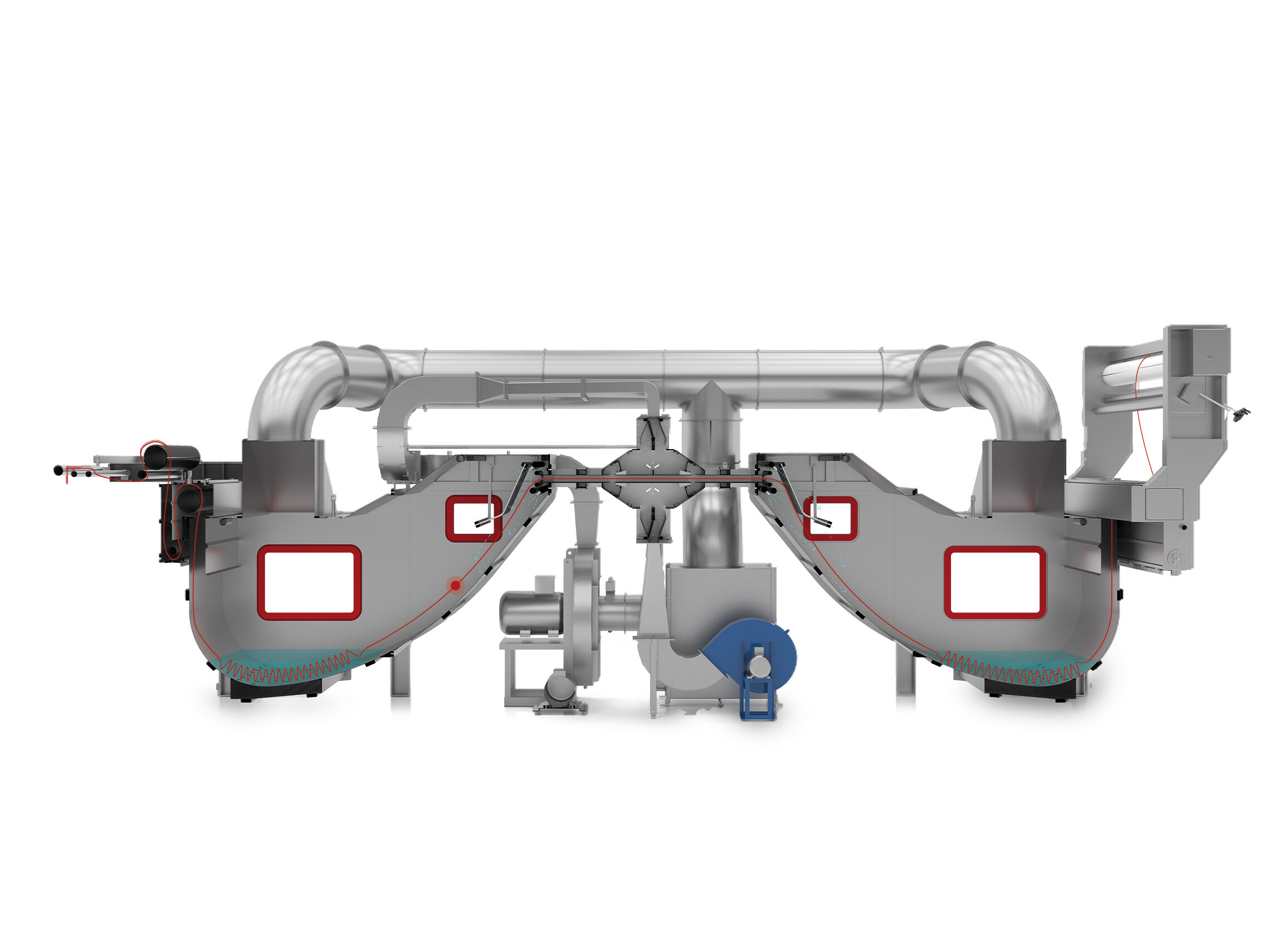
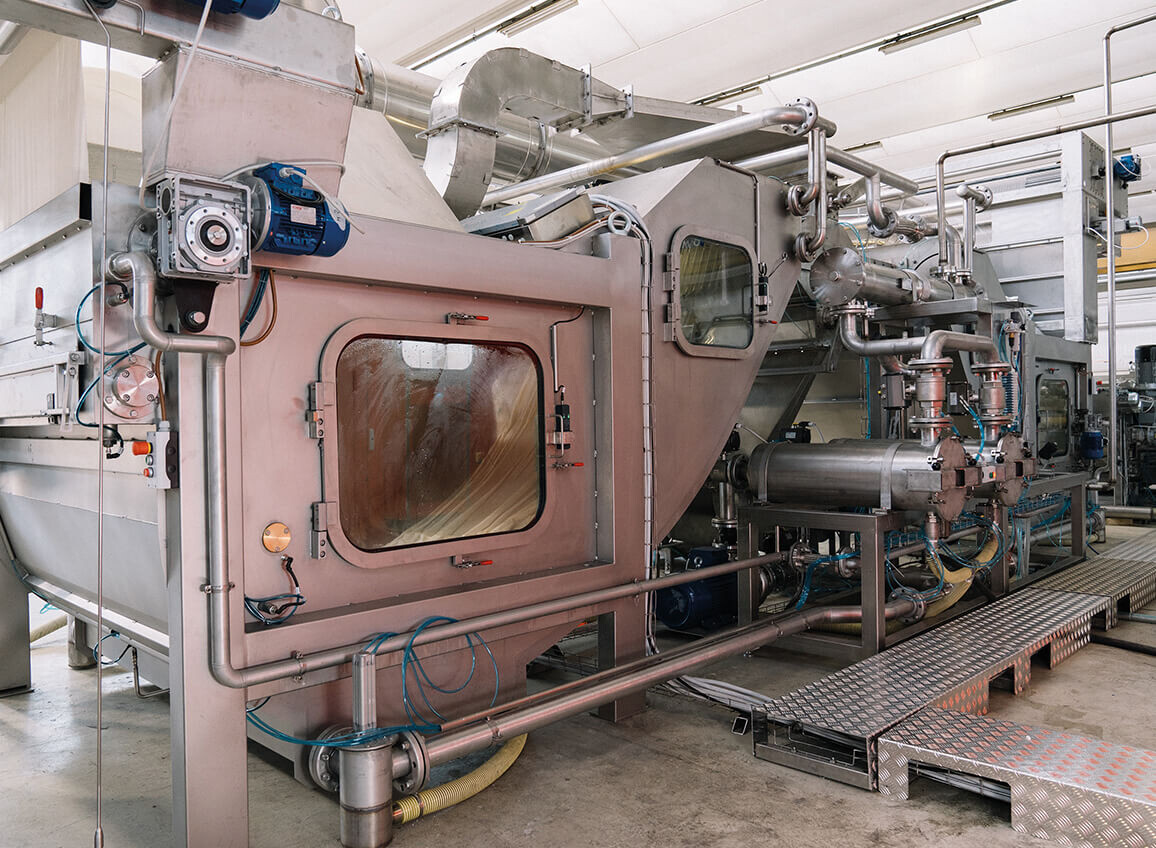
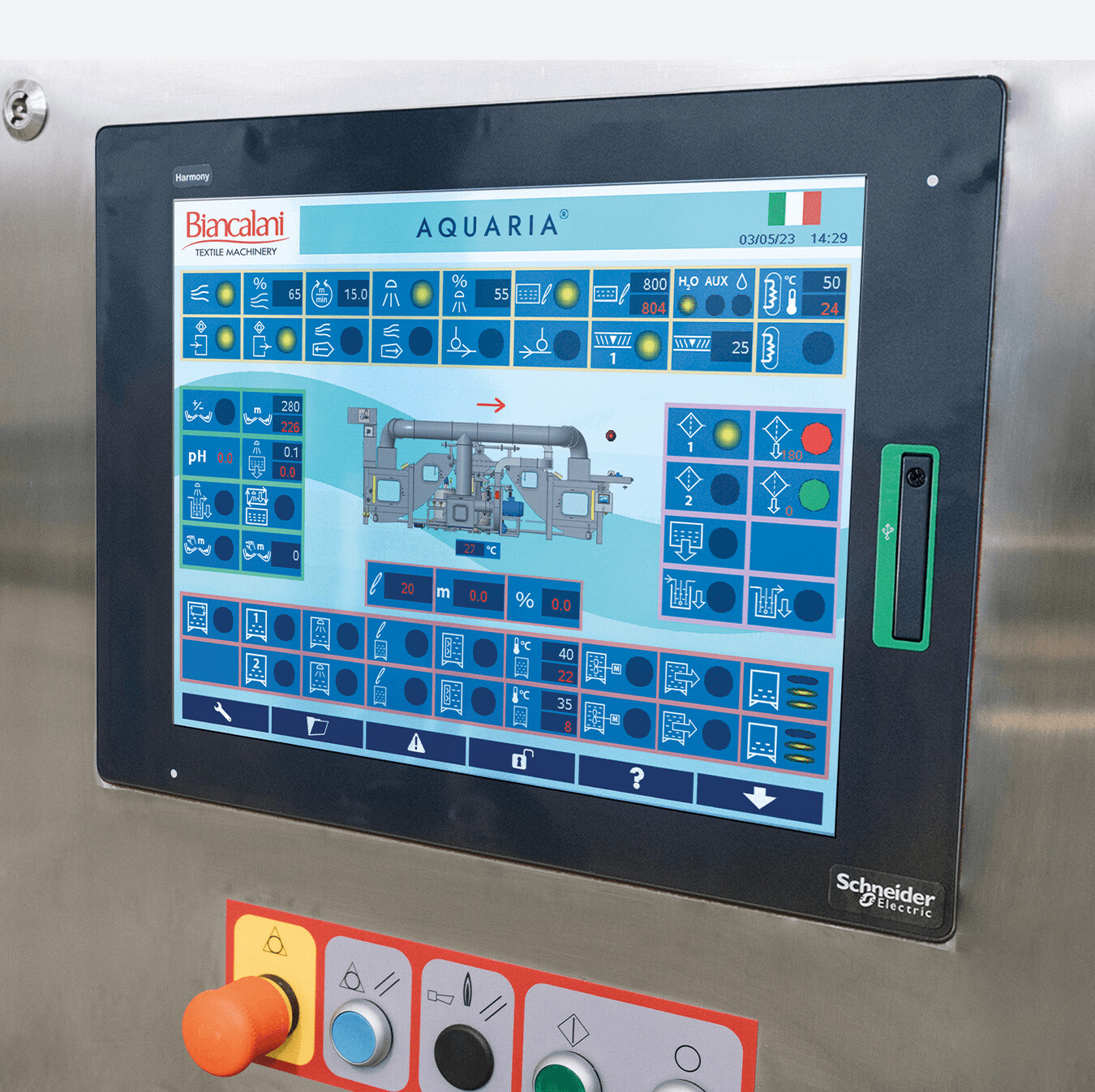
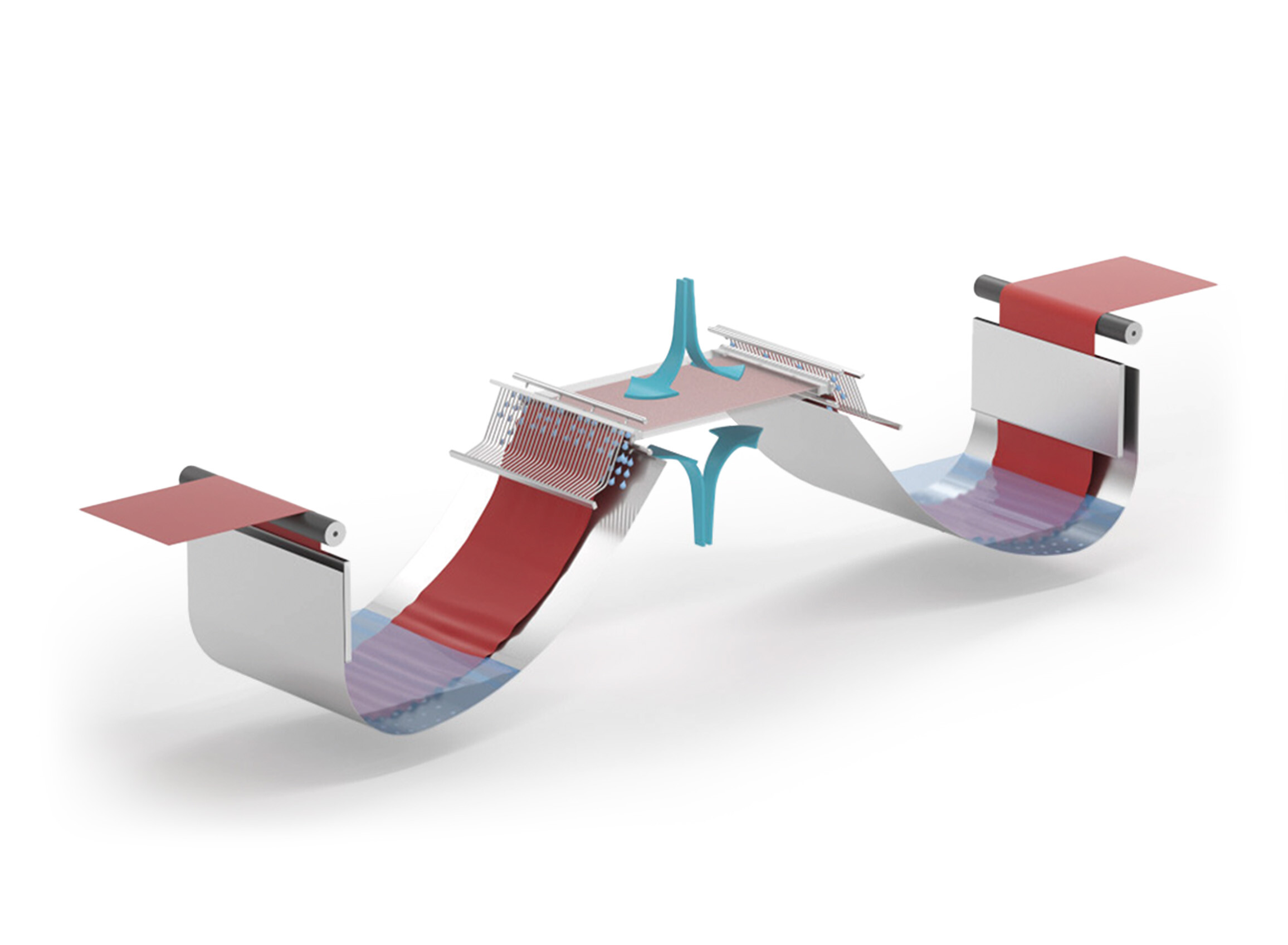
Here’s how it works
AQUARIA® is made up of two large accumulation chambers, connected by a pneumatic ejector (the treatment channel), with impact grills at its ends. Fabric moves at high speed inside the channel, impacts against the grids, and accumulates inside the chambers, where it can lay immersed in the process bath. A continuous nebulisation of the process bath through sprayers placed at each side of treatment channel keeps the fabric permanently and uniformly wet.
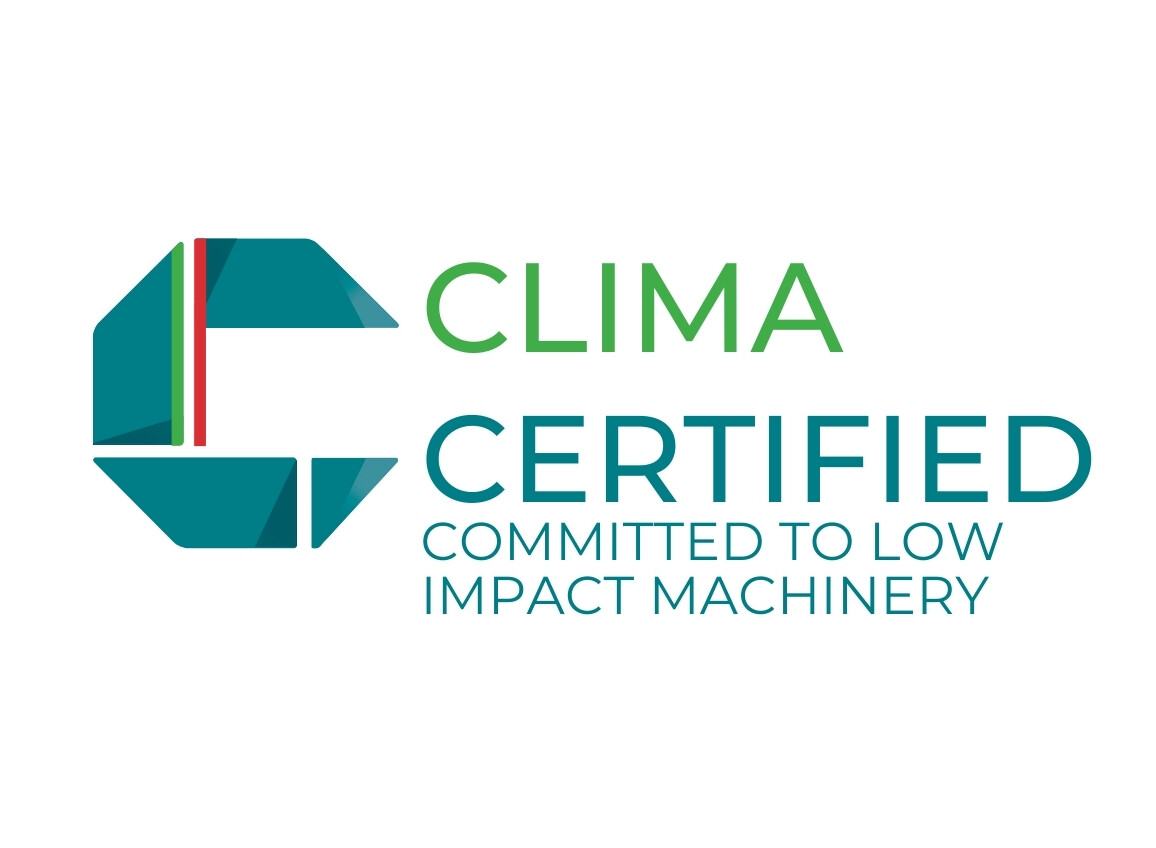
Efficient washing with variable water level
The power of air pushes the process bath inside the treatment channel and through the fabric, forcing it to penetrate deeply into the fibres. At the exit of the channel, the energetic impact against the grill quickly releases most of the water, for a continuous and efficient washing action.
This allows increasing the productivity of the washing line, while maintaining liquor ratio values as low as 1:6.
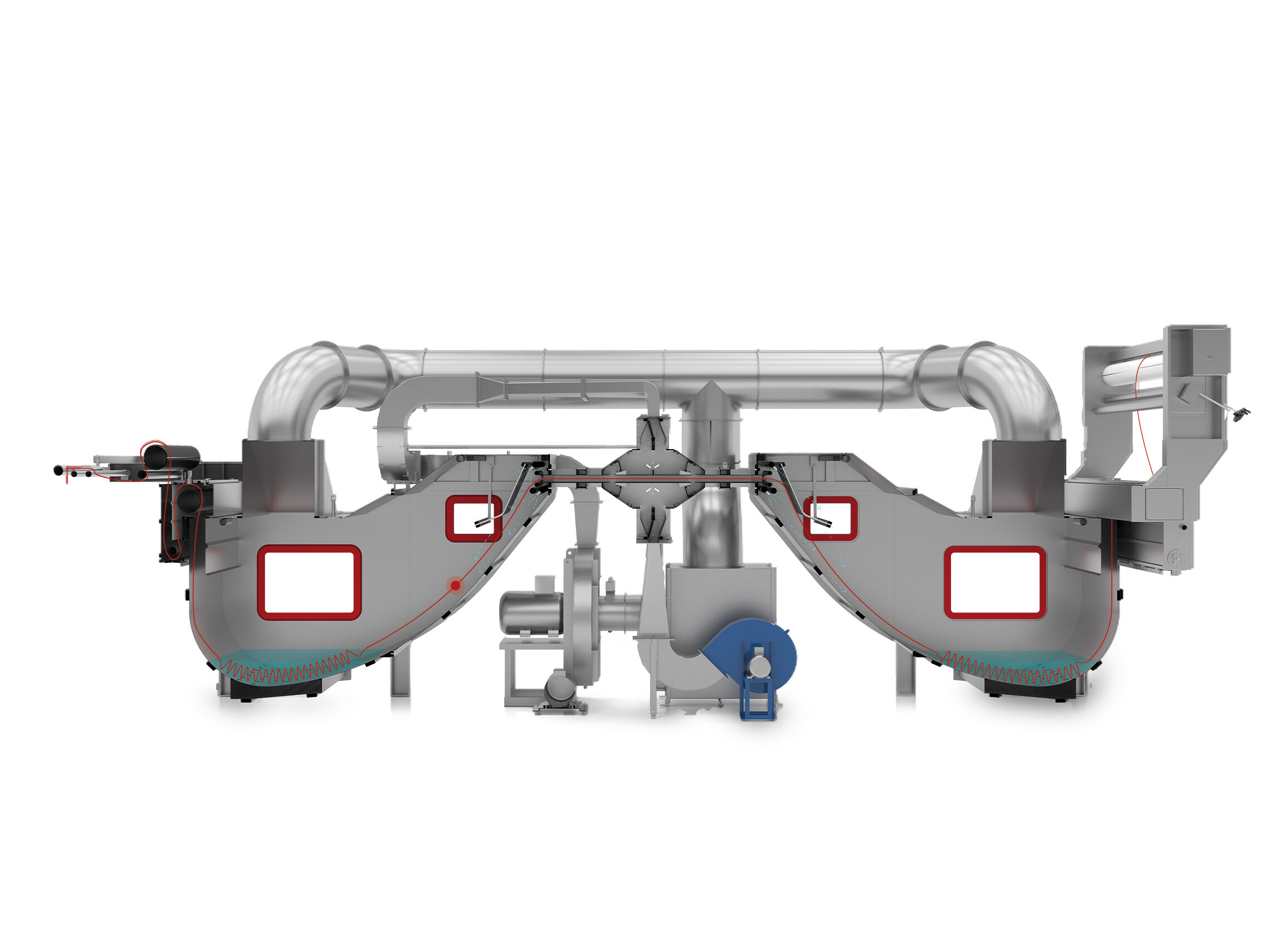
Extended adjustable dwell time and mechanical action
AQUARIA® is the only machine capable of processing open-width fabric at high speed, in complete safety, for a powerful mechanical action. At the same time, it offers very long dwell times, freely adjustable by varying the amount of fabric accumulation inside the machine.
This, together with the high exchange between air and water over the whole surface of the open width fabric, makes it ideal for continuous open-width enzyme treatments, and provides a fully sustainable approach to bleaching (AQUARIA® caustic-free eco-bleaching with zero-water discharge), scouring, and fashion effects.
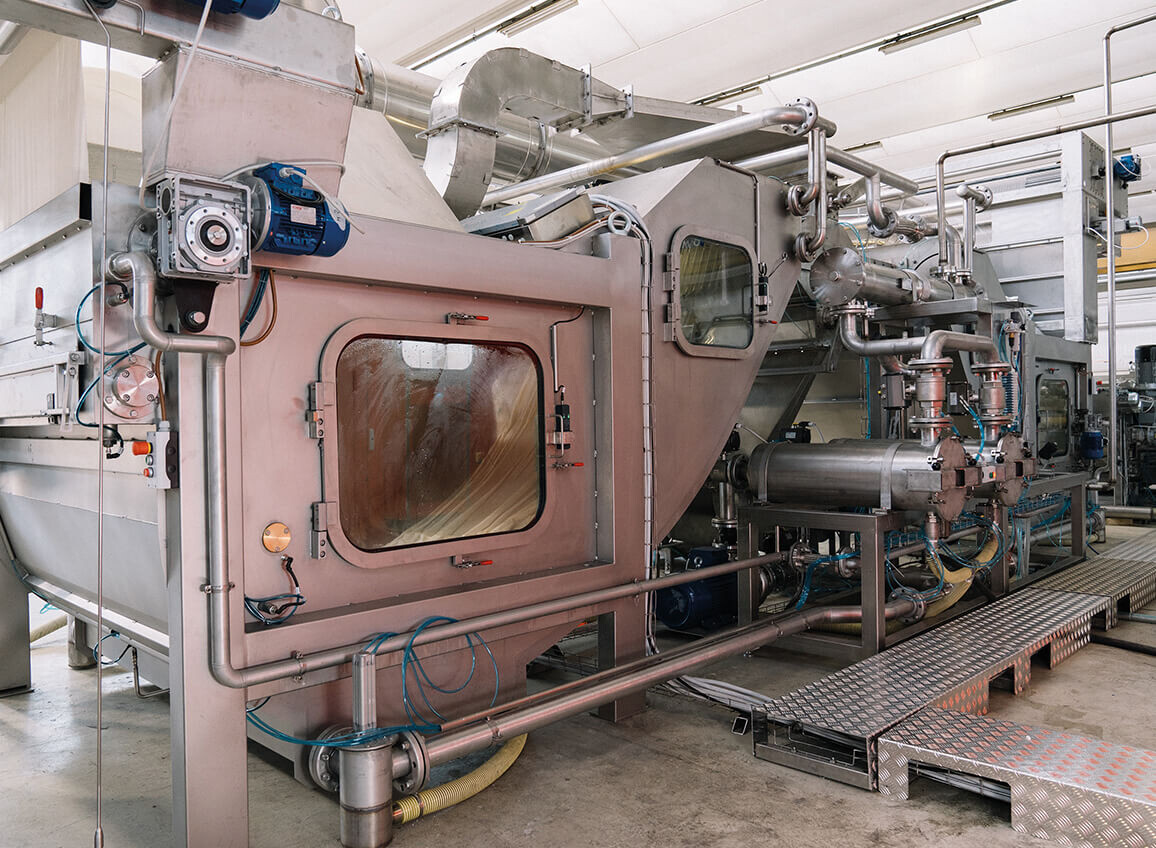
Well equipped for every need
High pressure and flow recirculation pumps, independent sprayers at the entrance of treatment channel inside the two accumulation chambers, indirect heating of the process bath for temperatures up to 98°C, water filtering devices, dosing systems for chemical products with controlled bath renewal and automatic level management: AQUARIA® includes everything for an automatized, efficient, and homogeneous wash.
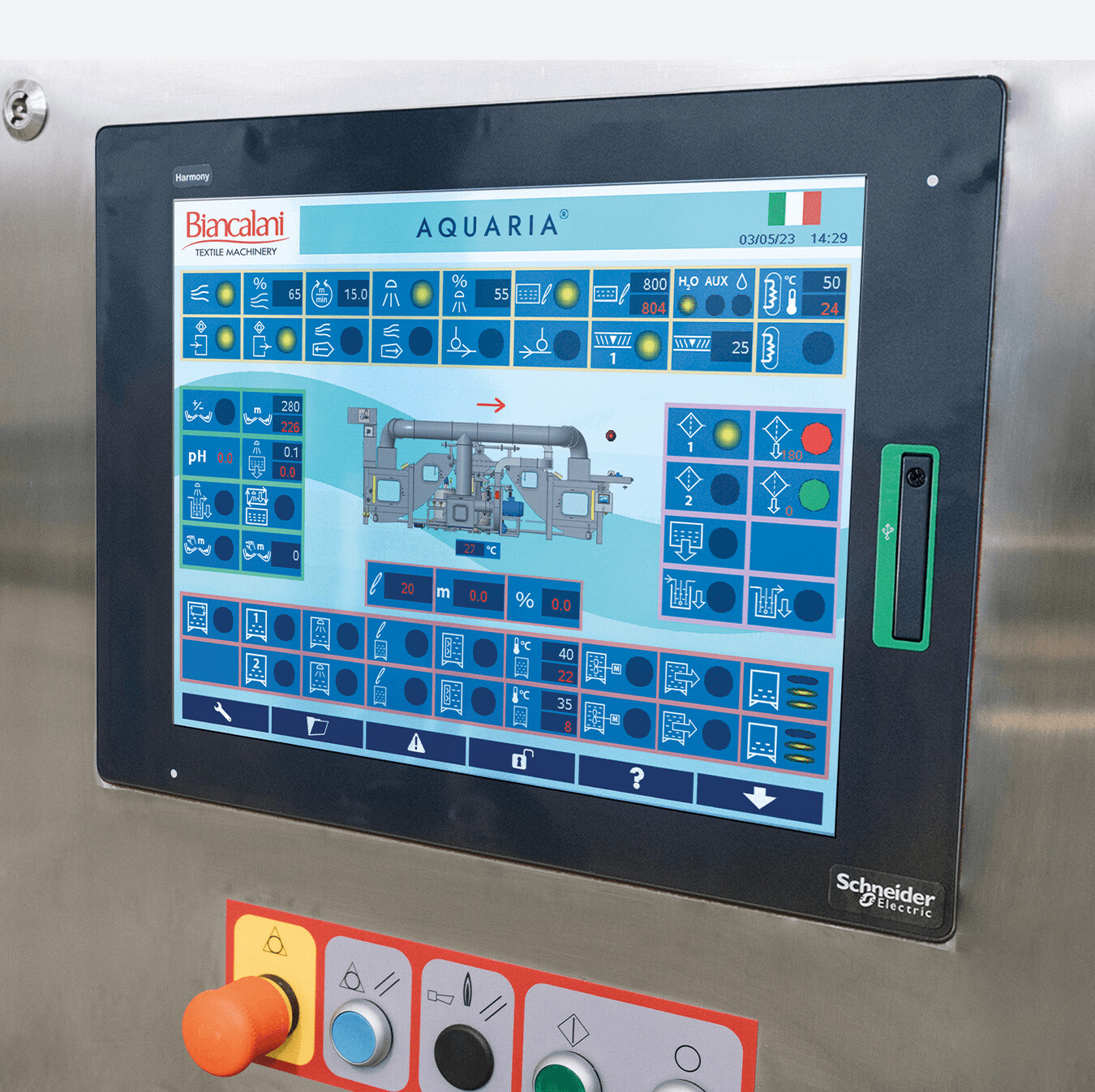
Perfect washing is a piece of cake!
A centralized touch screen, with auxiliary controls distributed over the whole line, and a simple user interface, provide complete control and storage into recipes of all the working parameters, as well as real-time monitoring of process data and utility consumptions for each process.
All the modules in the washing line are seamlessly interconnected and can be dynamically configured to offer a complete and versatile solution for any kind of wet processing.
Main AQUARIA® washing module in detail
Technical specifications
Available working widths | up to 3600 mm |
Water content | starting from 500 litres |
Dwell time | adjustable, by varying fabric content |
Fabric content | 20-500 m |
Production speed (fabric in/out) | 5-50 m/min (up to 80 m/min on request) |
Fabric treatment speed | up to 600 m/min |
Max. temperature of bath | 98°C |
Installed electrical power | from 90 kW |
Installed thermal power | from 550 kW |
Average utilization of steam | 500 kg/h (depending on process) |
Compressed air pressure | 6-10 bar |
Max consumption of compressed air | 500 Nl/min |
Dimensions (W x L x H) | from 3280 x 11600 x 3750 mm |
*The data shown can be changed at any time without prior notice due to product modification and improvement |
Auxiliary washing module
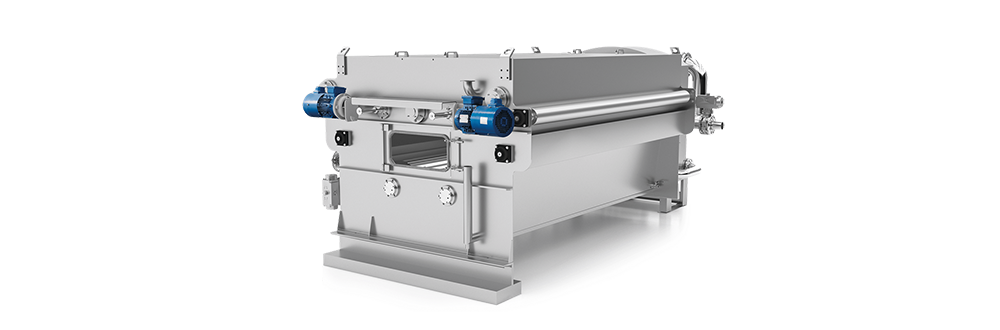
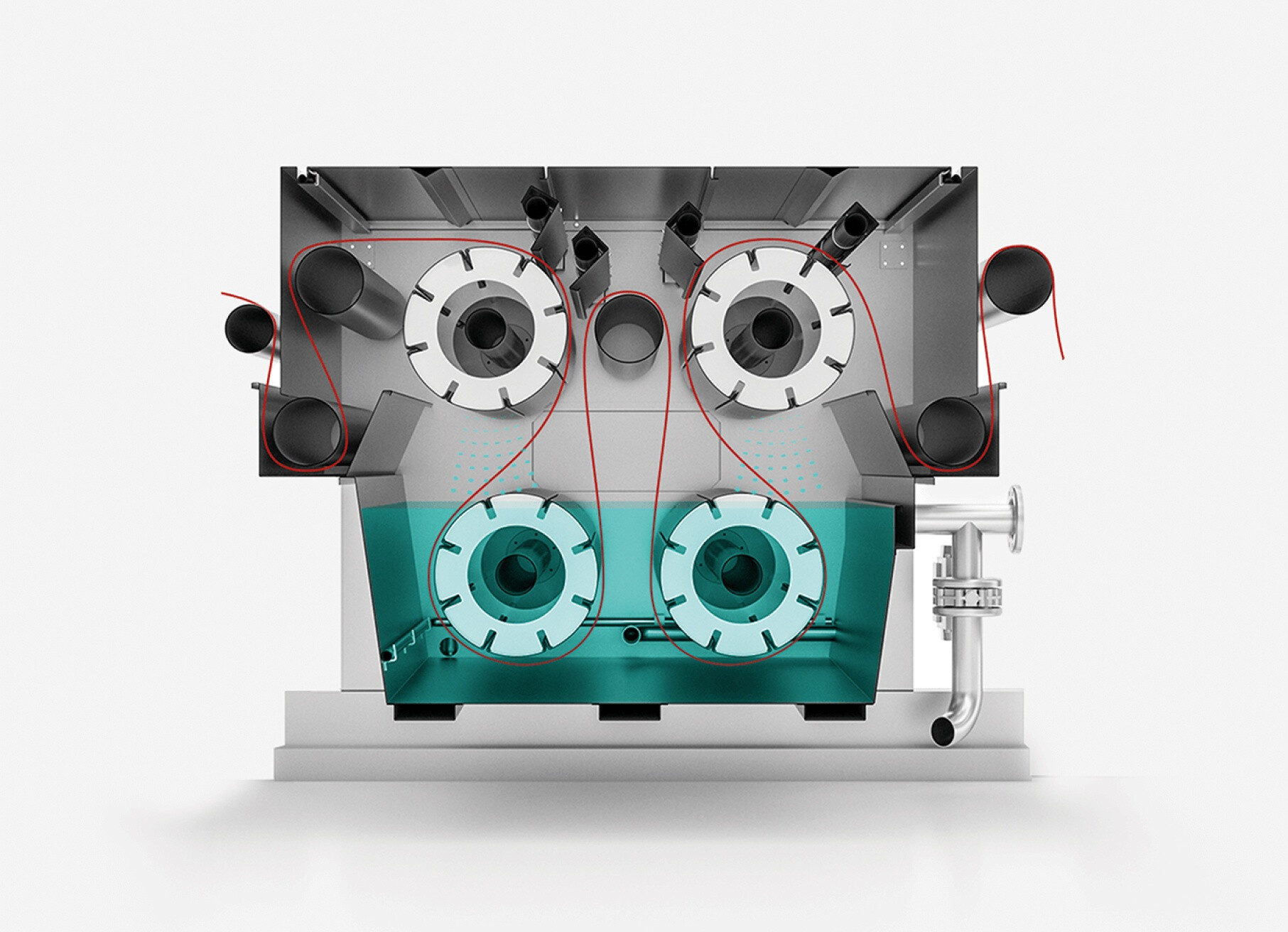
The icing on the cake
Pre-washing, soaping, rinsing, neutralization, application of chemicals... This versatile washing box complements the AQUARIA® washing line, and it can be installed – also in multiple units – before and after each AQUARIA® main module, in order to perform any additional steps required by each specific washing treatment.
Here’s how it works
Four large perforated cylinders guide the fabric inside the module, controlling the tension with load cells. High-speed bath recirculation is provided by a pump feeding a total of four powerful water blades which are installed over the two upper cylinders. The bath can be filtered and heated, while an overflow system maintains the level defining its renewal ratio, and a squeezing system extracts the excess water before delivering the fabric to the following module.
Build your line up, bring wastage down
This washing box can perform preliminary processes, which are auxiliary to the main treatment, when installed before the AQUARIA® main module, while when it is placed after it, allows to neutralize or rinse the chemical products that have been applied.
Several modules (each fitted with an integrated squeezing section) can be installed and connected to each other, in order to increase the washing efficiency and the productivity of the line, and to allow to redirecting the bath in counter-flow to previous modules (including AQUARIA® for optimization of water usage.
In line and well connected
As well as all the other components of the AQUARIA® washing range, also this auxiliary washing box is completely integrated within the line, and controlled through the main touch screen and auxiliary controls which offer real-time monitoring of process parameters and utility consumption, as well as easy management and storage into recipes of all working parameters.
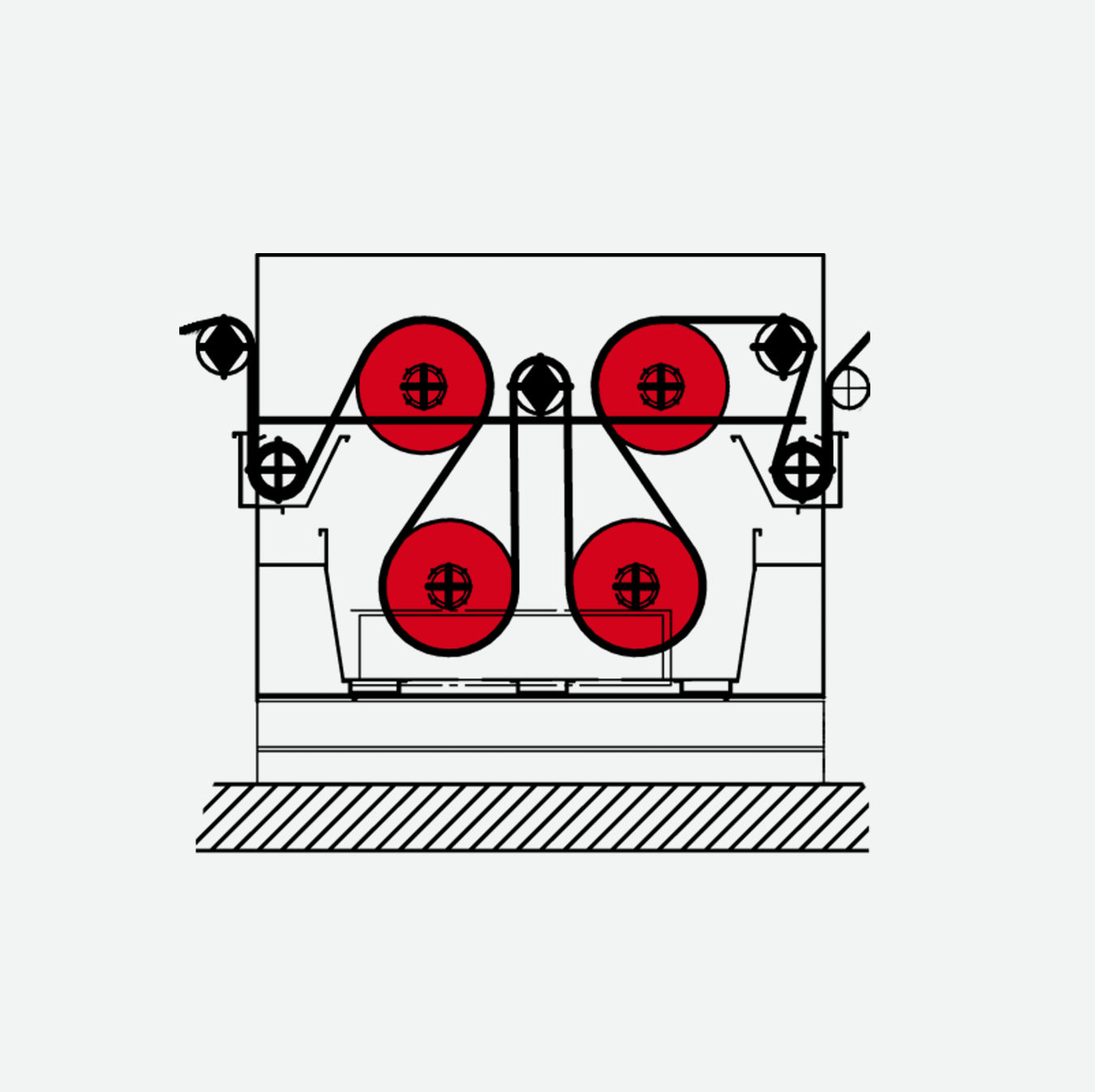
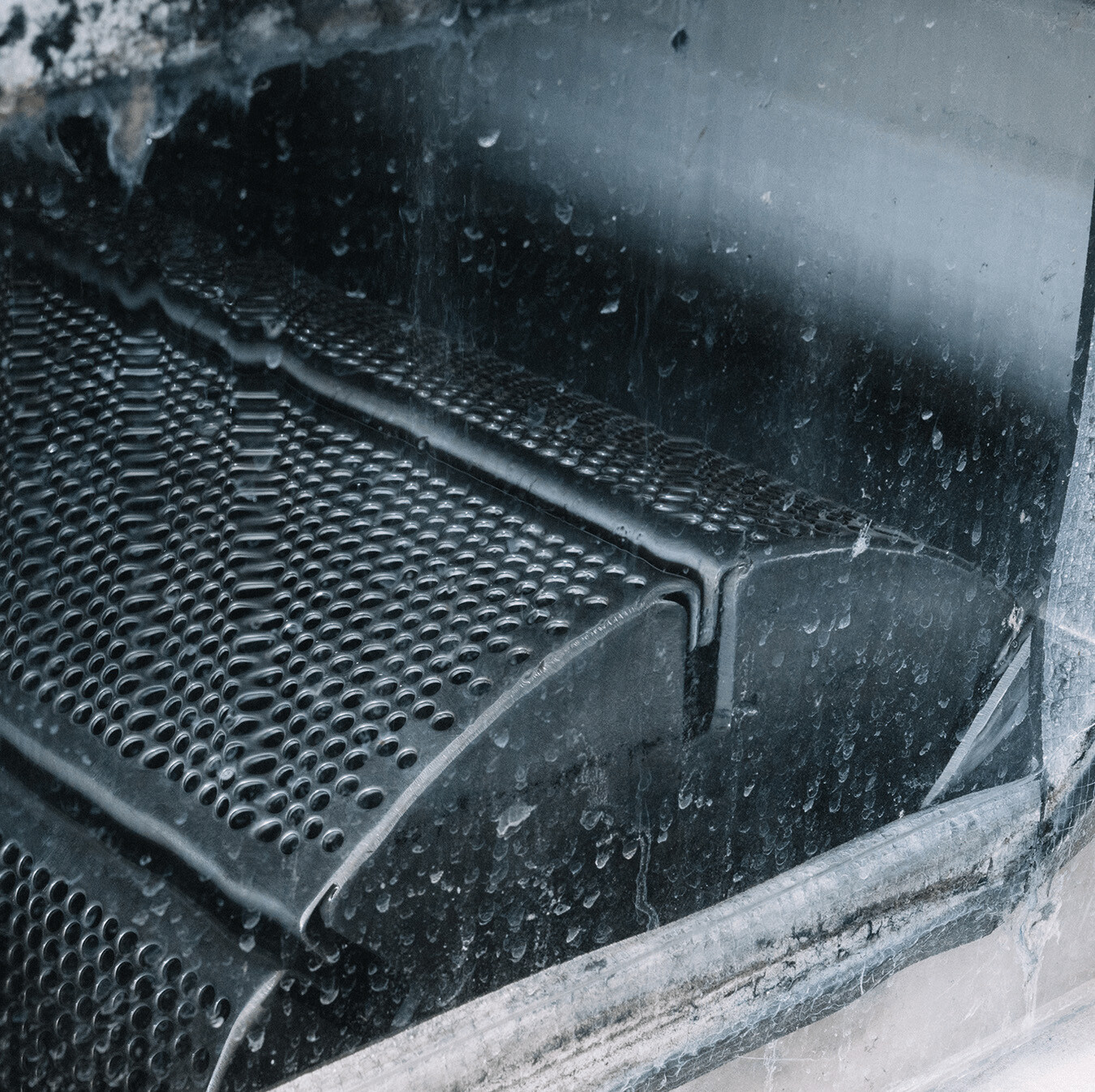
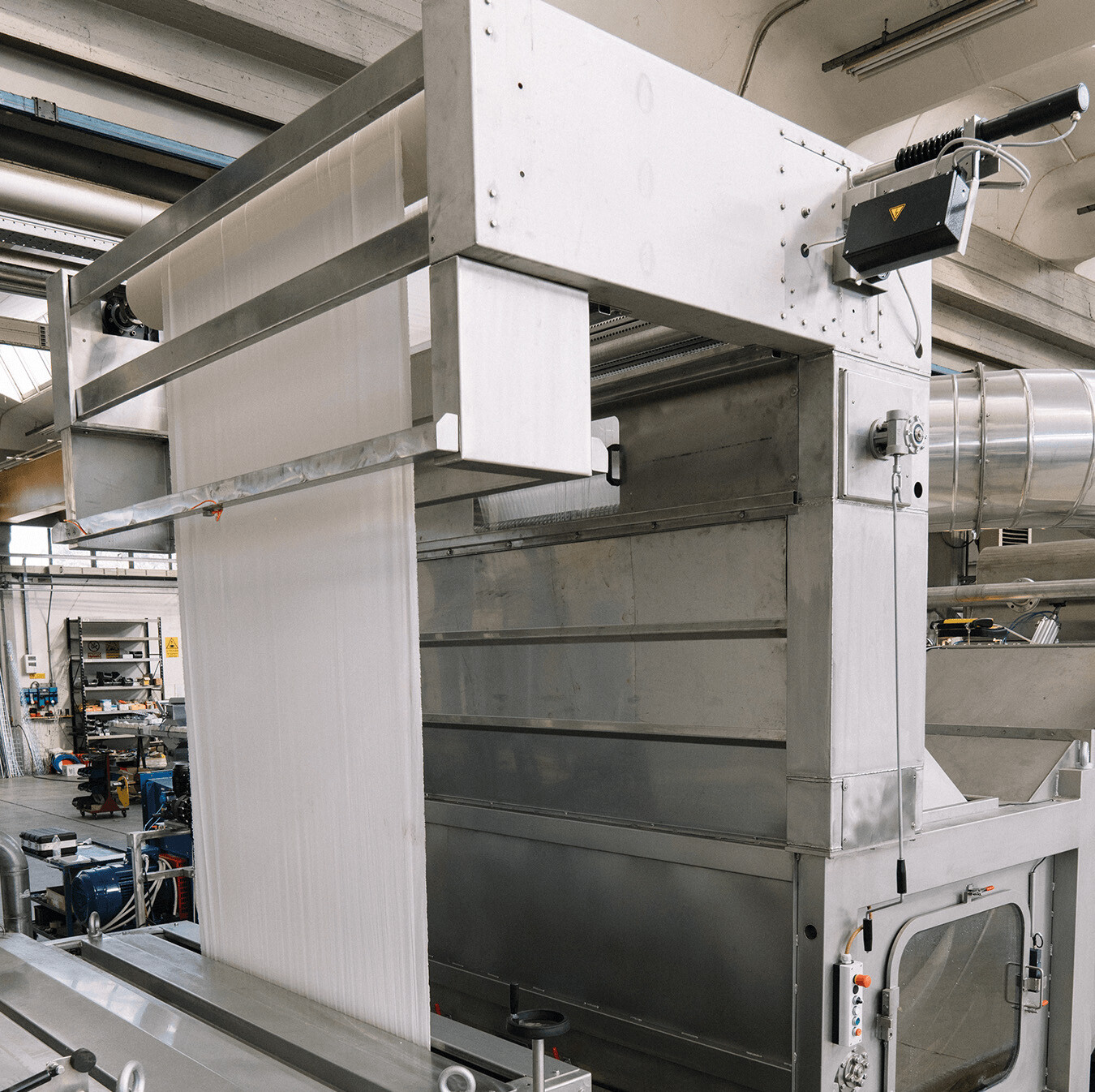
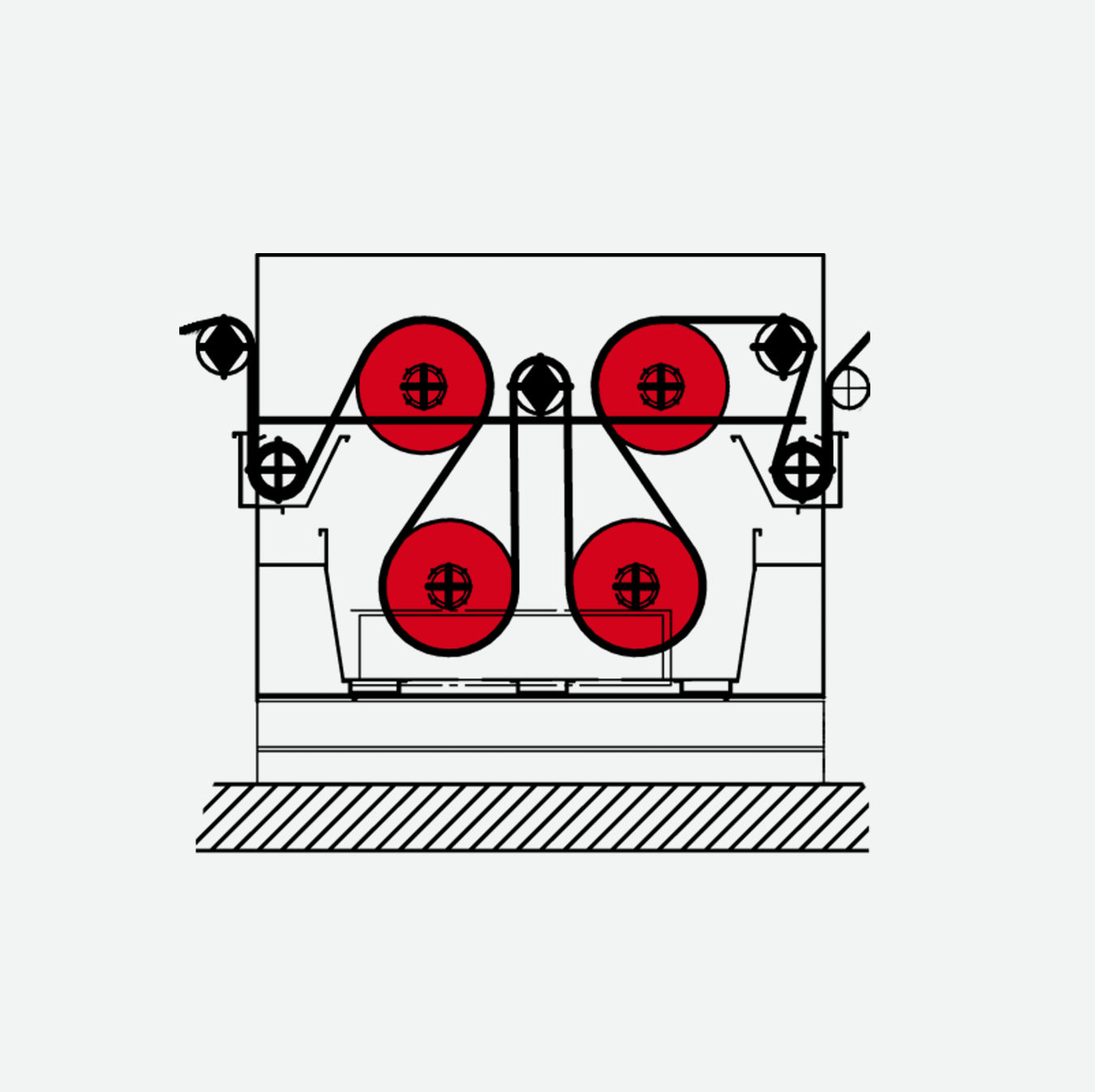
Here’s how it works
Four large perforated cylinders guide the fabric inside the module, controlling the tension with load cells. High-speed bath recirculation is provided by a pump feeding a total of four powerful water blades which are installed over the two upper cylinders. The bath can be filtered and heated, while an overflow system maintains the level defining its renewal ratio, and a squeezing system extracts the excess water before delivering the fabric to the following module.
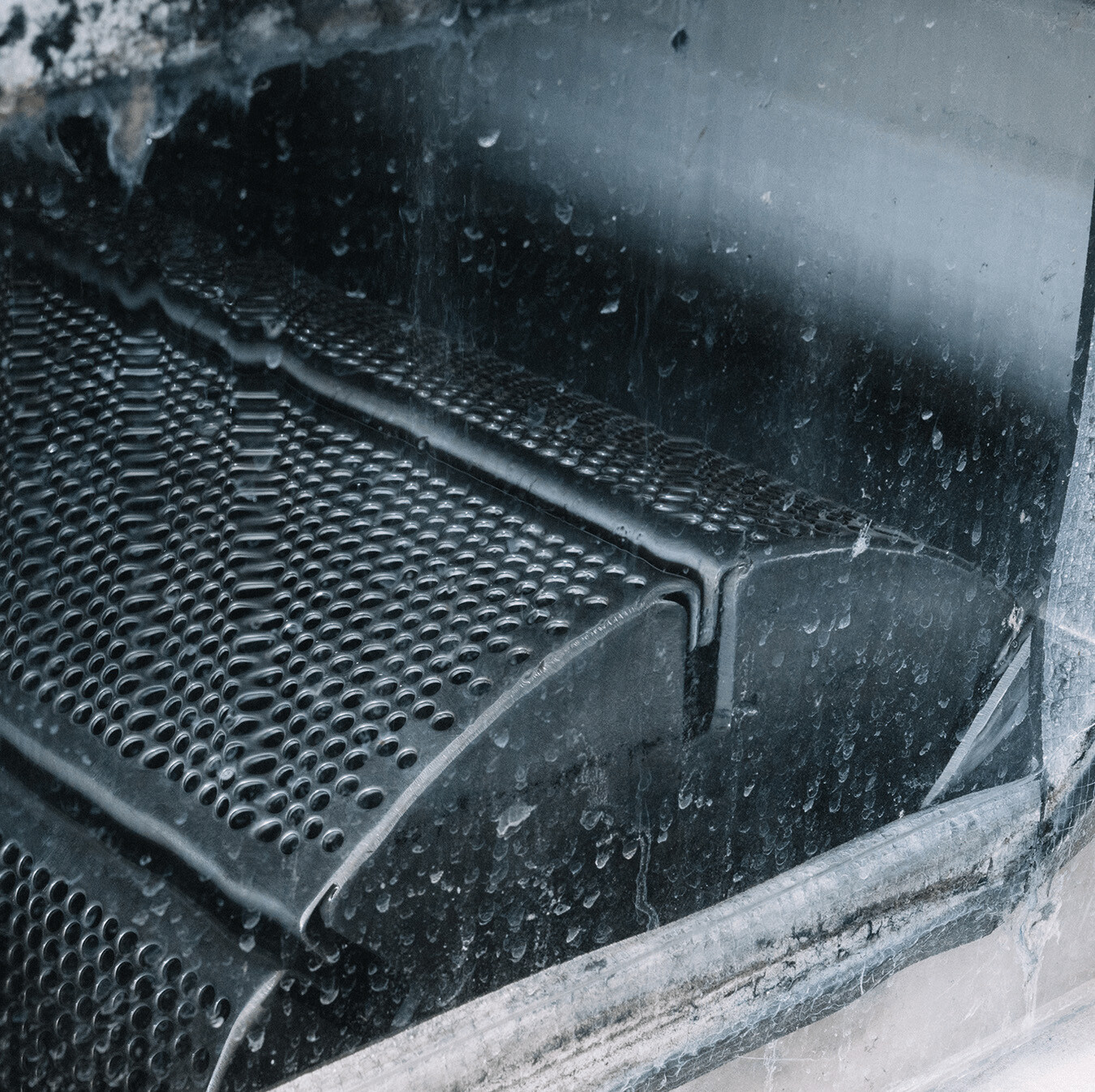
Build your line up, bring wastage down
This washing box can perform preliminary processes, which are auxiliary to the main treatment, when installed before the AQUARIA® main module, while when it is placed after it, allows to neutralize or rinse the chemical products that have been applied.
Several modules (each fitted with an integrated squeezing section) can be installed and connected to each other, in order to increase the washing efficiency and the productivity of the line, and to allow to redirecting the bath in counter-flow to previous modules (including AQUARIA® for optimization of water usage.
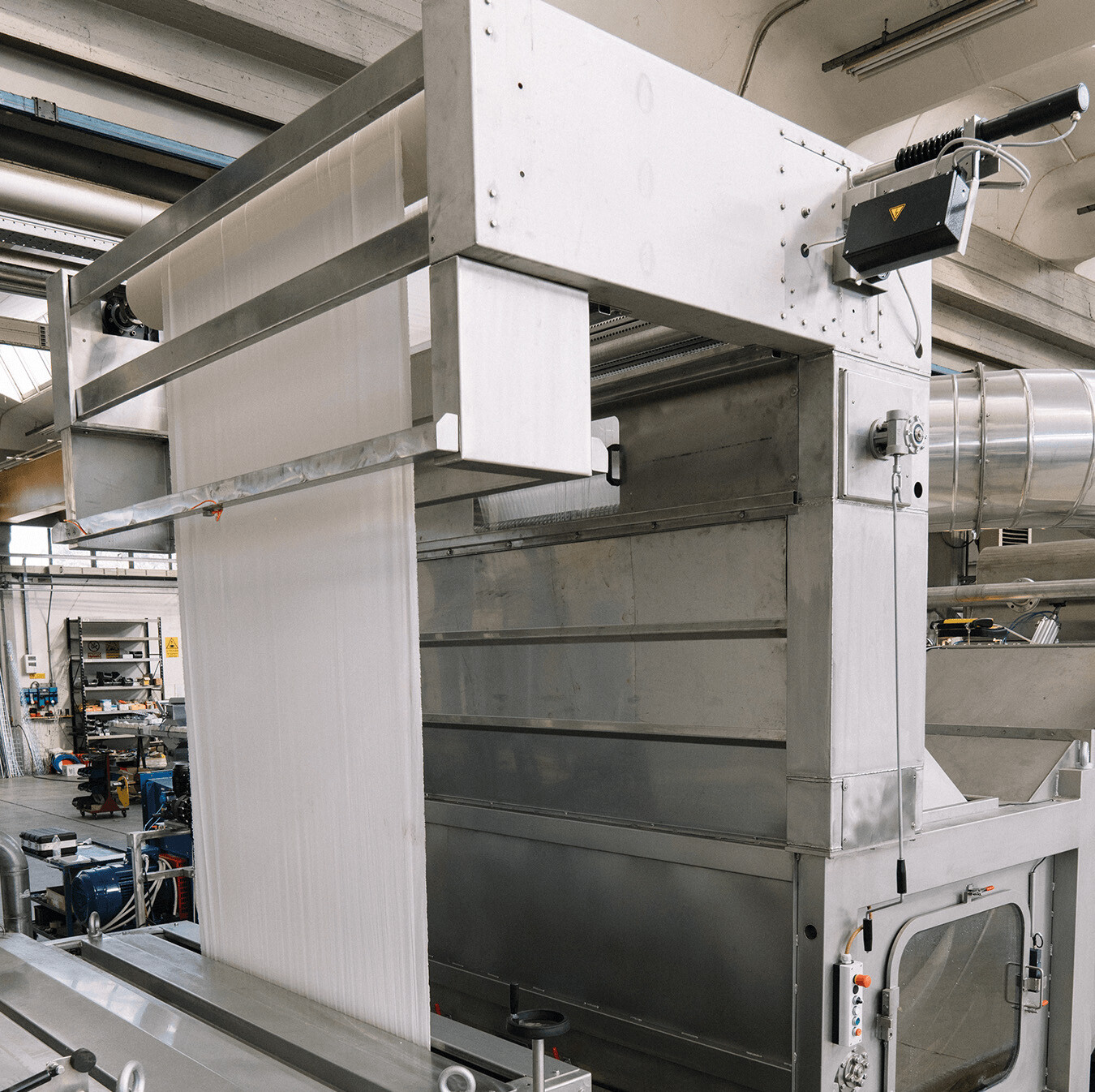
In line and well connected
As well as all the other components of the AQUARIA® washing range, also this auxiliary washing box is completely integrated within the line, and controlled through the main touch screen and auxiliary controls which offer real-time monitoring of process parameters and utility consumption, as well as easy management and storage into recipes of all working parameters.
Auxiliary module in detail
Technical specifications
Available working widths | up to 3600 mm |
Water content | starting from 700 litres |
Fabric content | 5 m |
Production speed (fabric in/out) | 5-50 m/min (up to 80 m/min on request) |
Max. temperature of bath | 90°C with optional heating system |
Installed electrical power | from 14 kW |
Installed thermal power | from 500 kW |
Average utilization of steam | 500 kg/h (depending on process) |
Dimensions (W x L x H) | from 2400 x 3600 x 2100 mm |
*The data shown can be changed at any time without prior notice due to product modification and improvement |
Additional devices and options
Squeezing sections
Installed as independent unit in the line or integrated at the exit of each auxiliary washing module, these water extraction sections are offered with different squeezing pressures according to their position. Installed in the AQUARIA® line between two washing sections, with a linear squeezing pressure of 12 kg/cm they provide an efficient way to extract and re-route the water back to any previous module. When installed at the exit of the washing line, a higher squeezing pressure (i.e. 50 kg/cm) ensures to extract and possibly recycle the highest possible amount of water before fabric delivery. On request other types of water extraction devices, such as vacuum units, can also be supplied.
Preparation tanks and direct dosing pumps
The AQUARIA® line can be fitted with multiple systems for automatically dosing and routing any type of chemical products to provide each module with the right amount of solution at the right time.
A set of two tanks can be used to prepare, mix, dilute and preheat any chemical solution, which is then automatically introduced into the washing modules following the required dilution percentage in order to control bath reintegration and water exchange. In parallel, other dosing systems can be used to accurately dispense dry products (granular, powders, etc.) as well a modular system of multiple volumetric pumps which can determine the correct amount of chemical solutions and introduce them directly from their containers to the washing modules.
Bath filtering
All the modules in the AQUARIA® line can be fitted with different types of filters according to the needs and the requirements of the process. The standard cartridge type is installed on the bath recirculation circuit, and can be bypassed at any time for inspection and cleaning operations without interrupting the washing process. In addition, other types of filters are available for specific applications, such as – for instance – an oil separation device that efficiently extracts the oils removed during the scouring process.
Sensors and process control
Each detail of the process can be controlled with continuity and accuracy, thanks to the availability of several types of sensors and probes. From the level sensors, used to control the water exchange and reintegration, to the temperature probes installed on the recirculation pipes and inside the accumulation chamber of AQUARIA®, to optional sensors such as pH, ORP/Redox, and electrical conductivity.
Integrated reporting and diagnostic
Through a user-friendly interface, the touch screens allow for complete control of the whole AQUARIA® line. Recipes, usage statistics and real-time data for each individual module and for the whole line can be visualised and managed either locally or from a remote computer connected to the network. A complete diagnostic system immediately informs the user of possible issues detected at any point of the line, providing complete info in order to facilitate a quick and effective solution. AQUARIA® is also open to directly accessing all the working parameters in order to be interfaced with existing monitoring systems (i.e. industry 5.0).
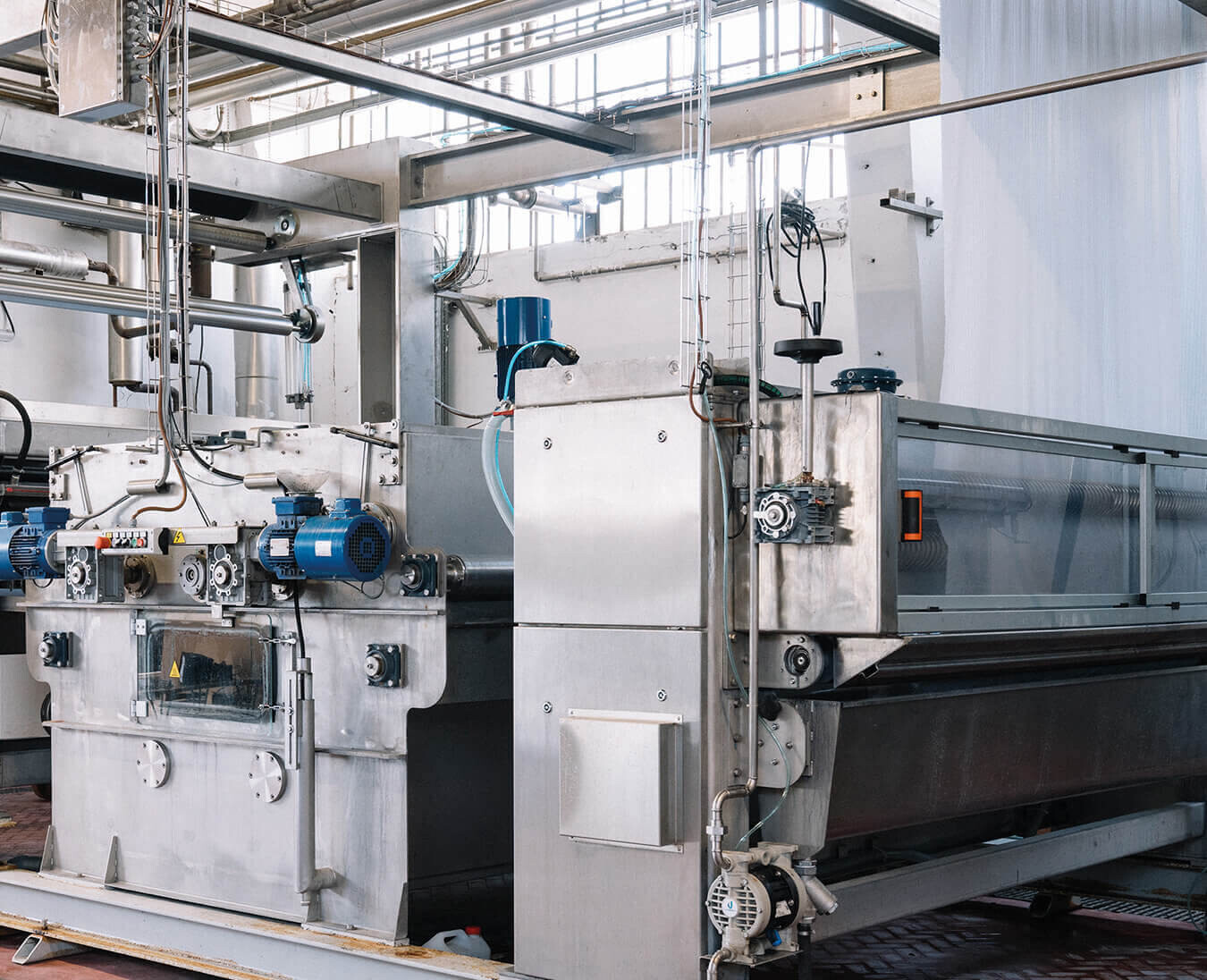
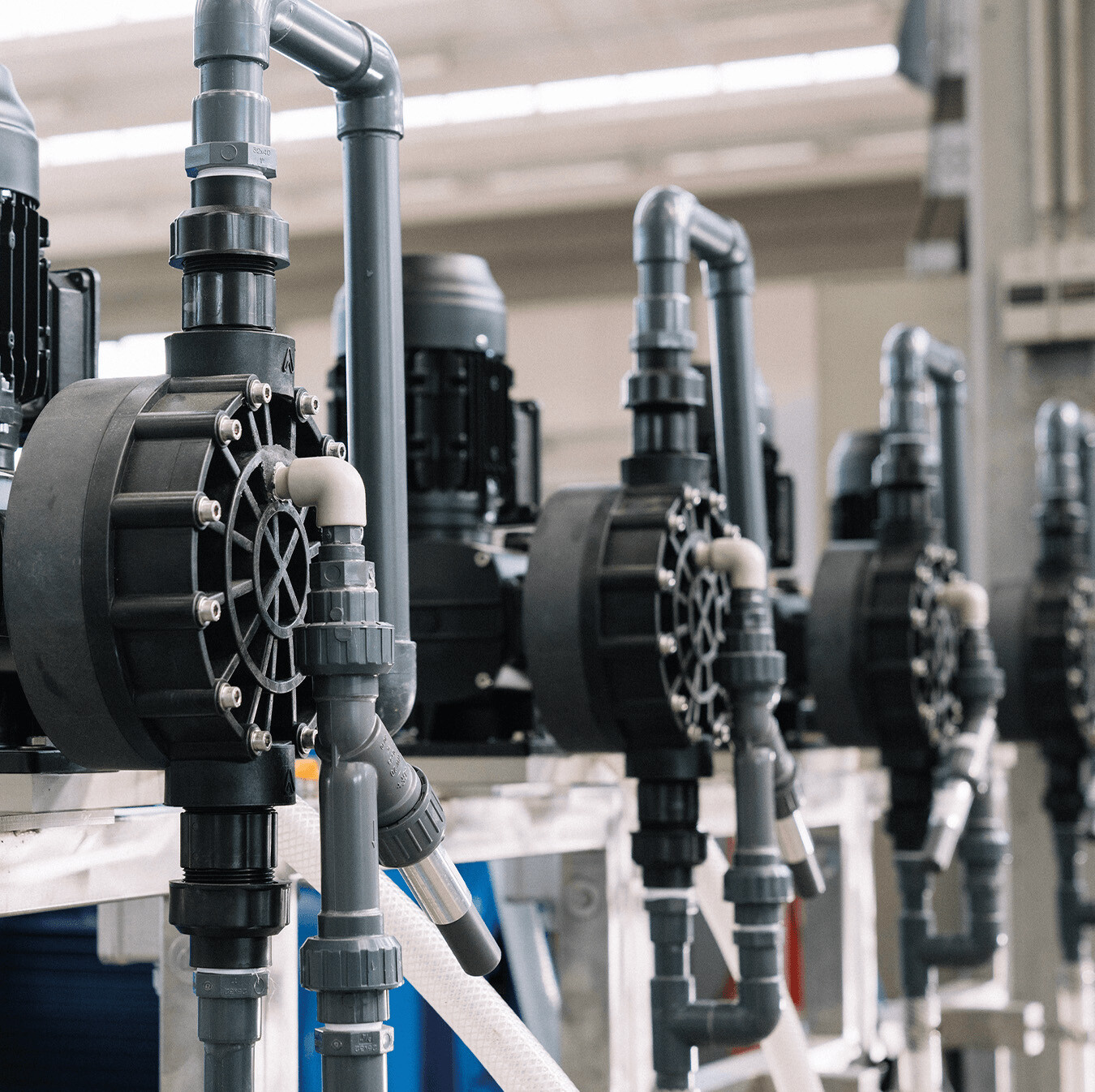
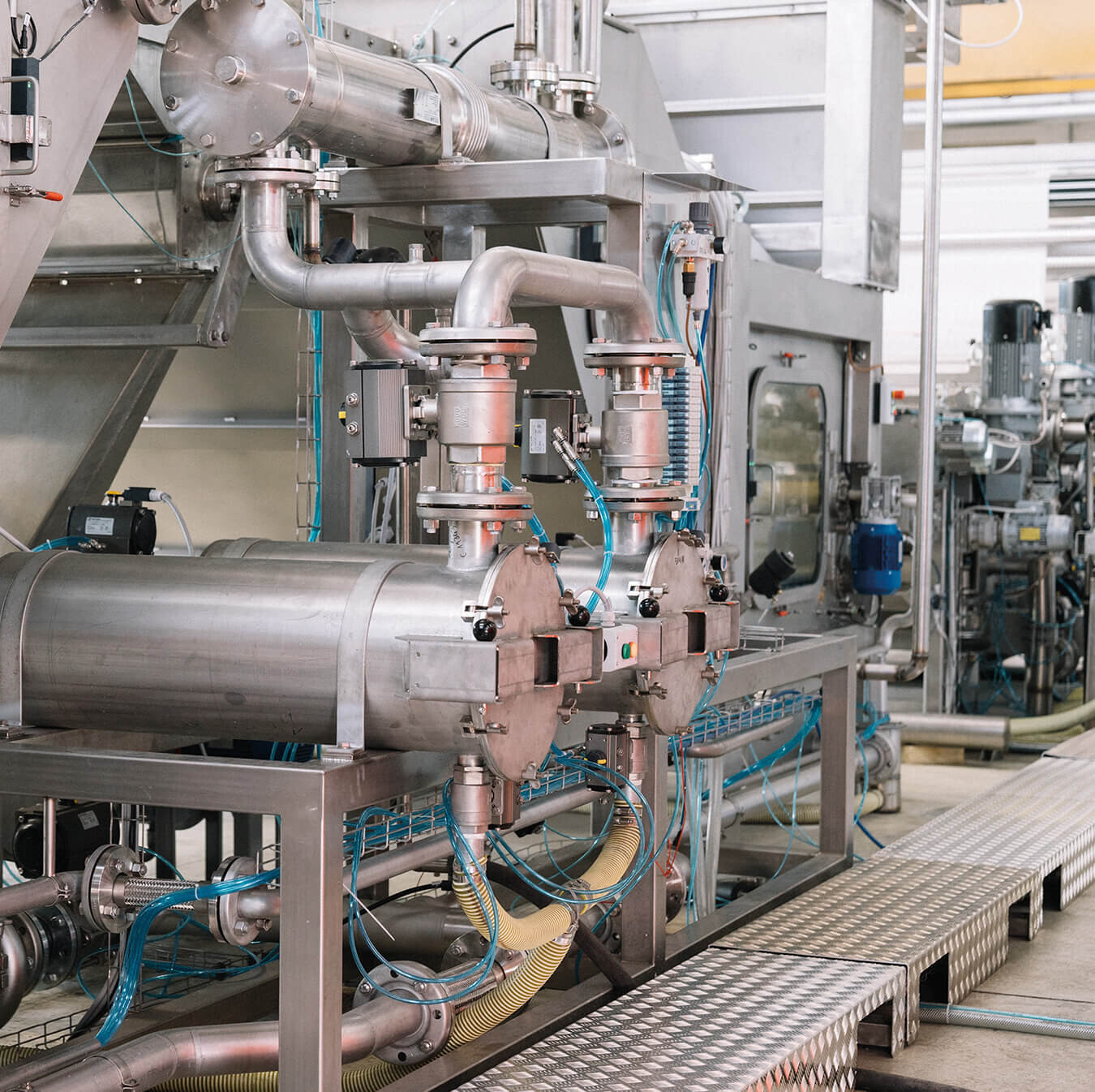
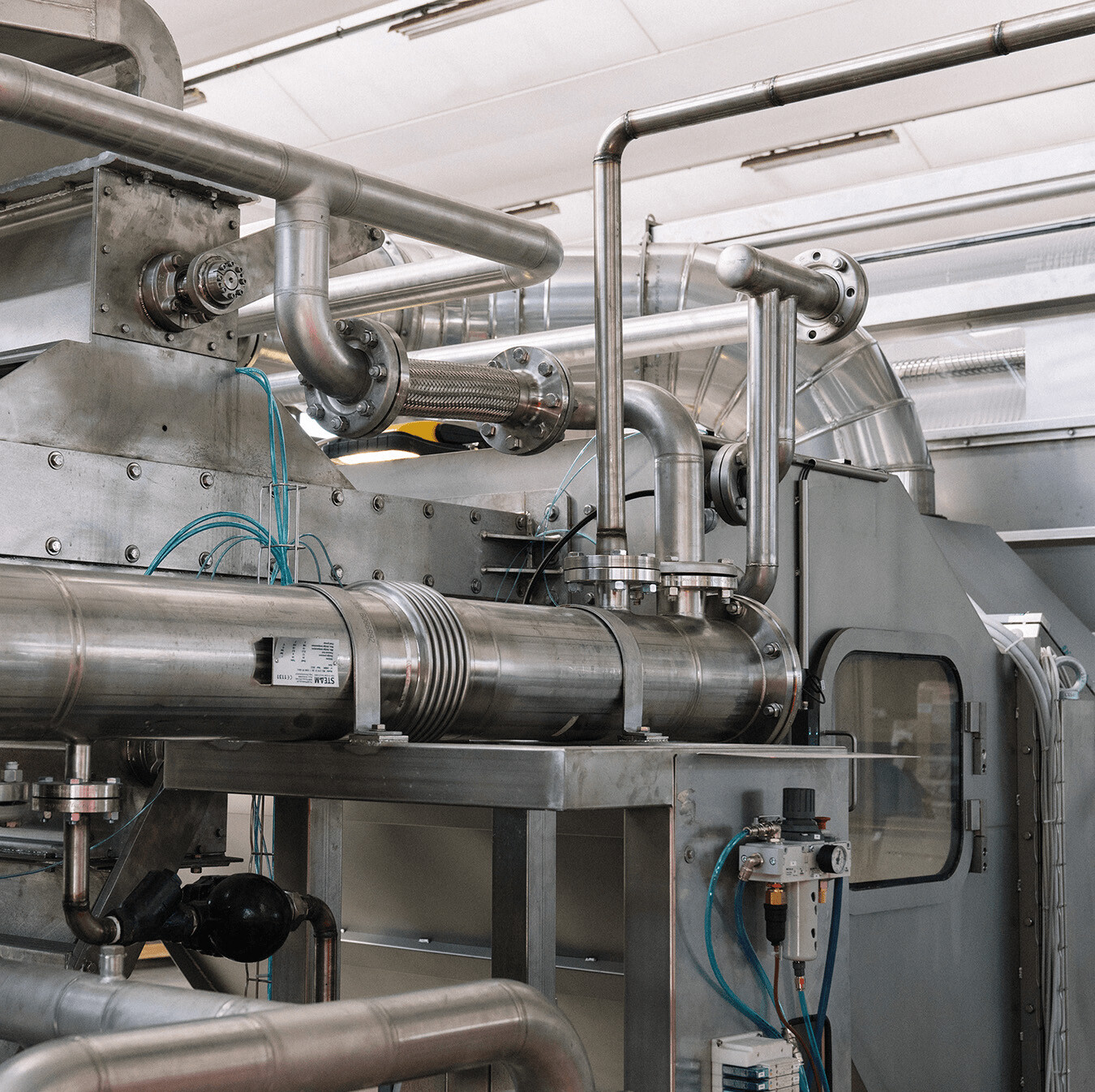
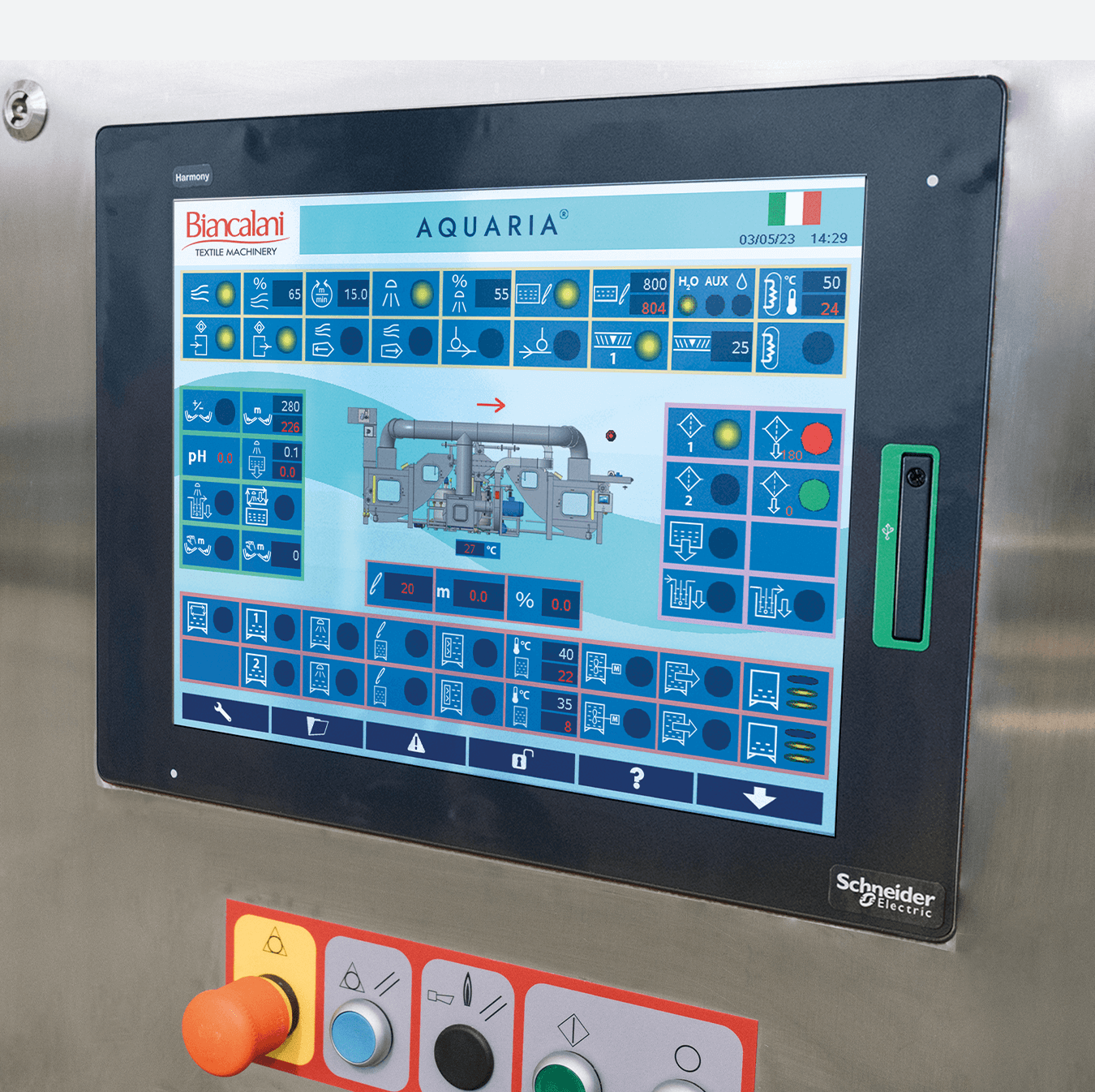
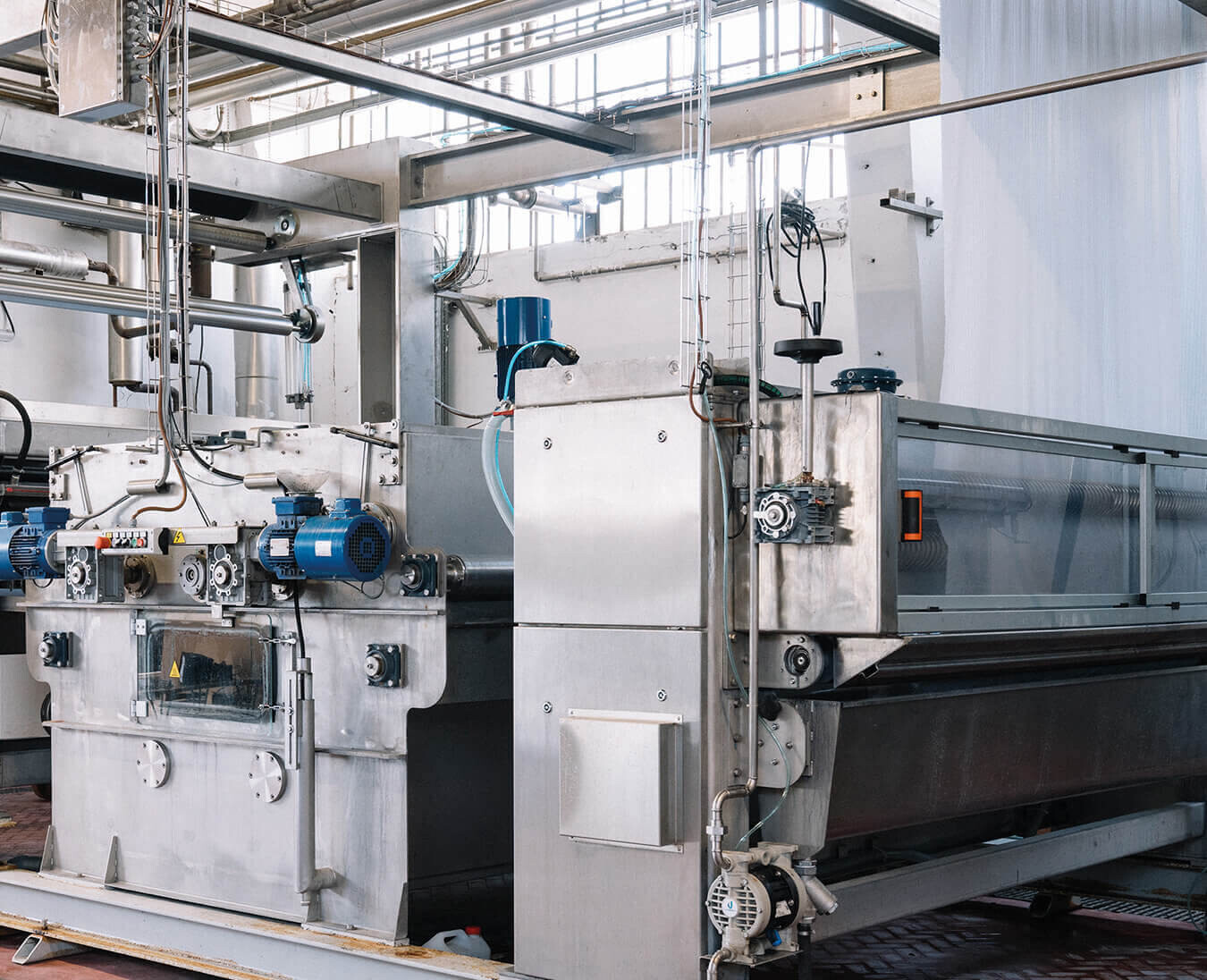
Squeezing sections
Installed as independent unit in the line or integrated at the exit of each auxiliary washing module, these water extraction sections are offered with different squeezing pressures according to their position. Installed in the AQUARIA® line between two washing sections, with a linear squeezing pressure of 12 kg/cm they provide an efficient way to extract and re-route the water back to any previous module. When installed at the exit of the washing line, a higher squeezing pressure (i.e. 50 kg/cm) ensures to extract and possibly recycle the highest possible amount of water before fabric delivery. On request other types of water extraction devices, such as vacuum units, can also be supplied.
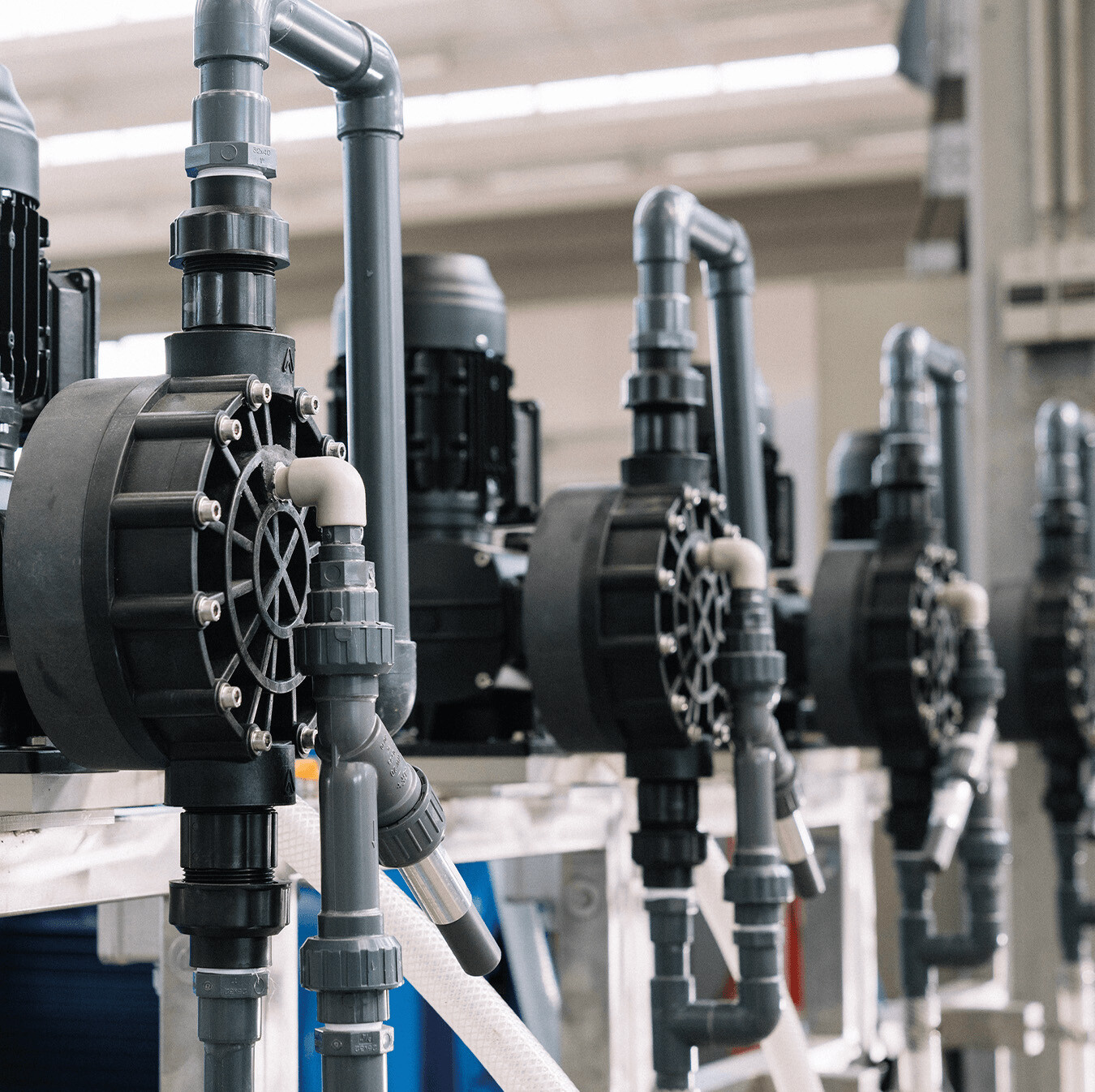
Preparation tanks and direct dosing pumps
The AQUARIA® line can be fitted with multiple systems for automatically dosing and routing any type of chemical products to provide each module with the right amount of solution at the right time.
A set of two tanks can be used to prepare, mix, dilute and preheat any chemical solution, which is then automatically introduced into the washing modules following the required dilution percentage in order to control bath reintegration and water exchange. In parallel, other dosing systems can be used to accurately dispense dry products (granular, powders, etc.) as well a modular system of multiple volumetric pumps which can determine the correct amount of chemical solutions and introduce them directly from their containers to the washing modules.
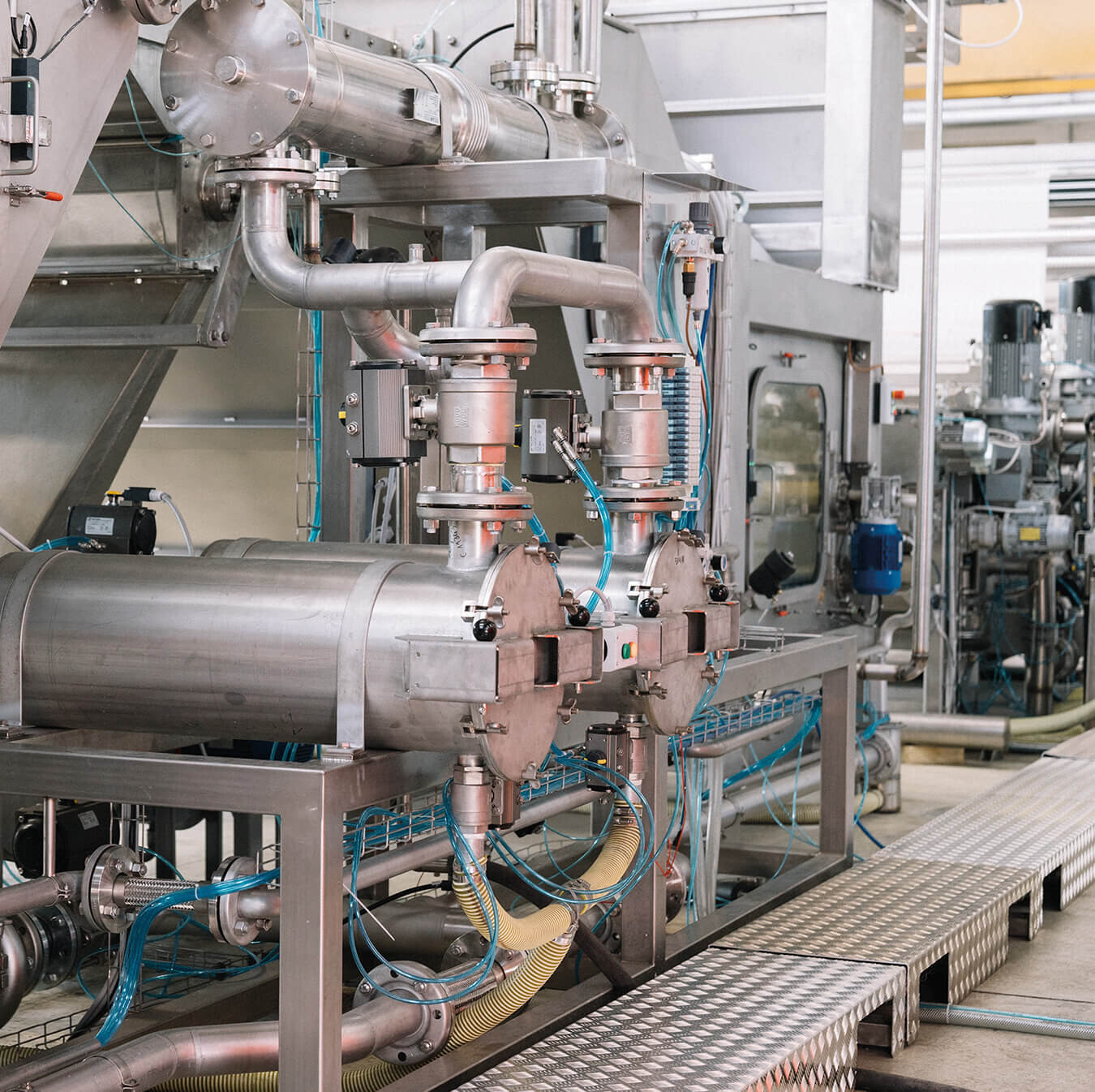
Bath filtering
All the modules in the AQUARIA® line can be fitted with different types of filters according to the needs and the requirements of the process. The standard cartridge type is installed on the bath recirculation circuit, and can be bypassed at any time for inspection and cleaning operations without interrupting the washing process. In addition, other types of filters are available for specific applications, such as – for instance – an oil separation device that efficiently extracts the oils removed during the scouring process.
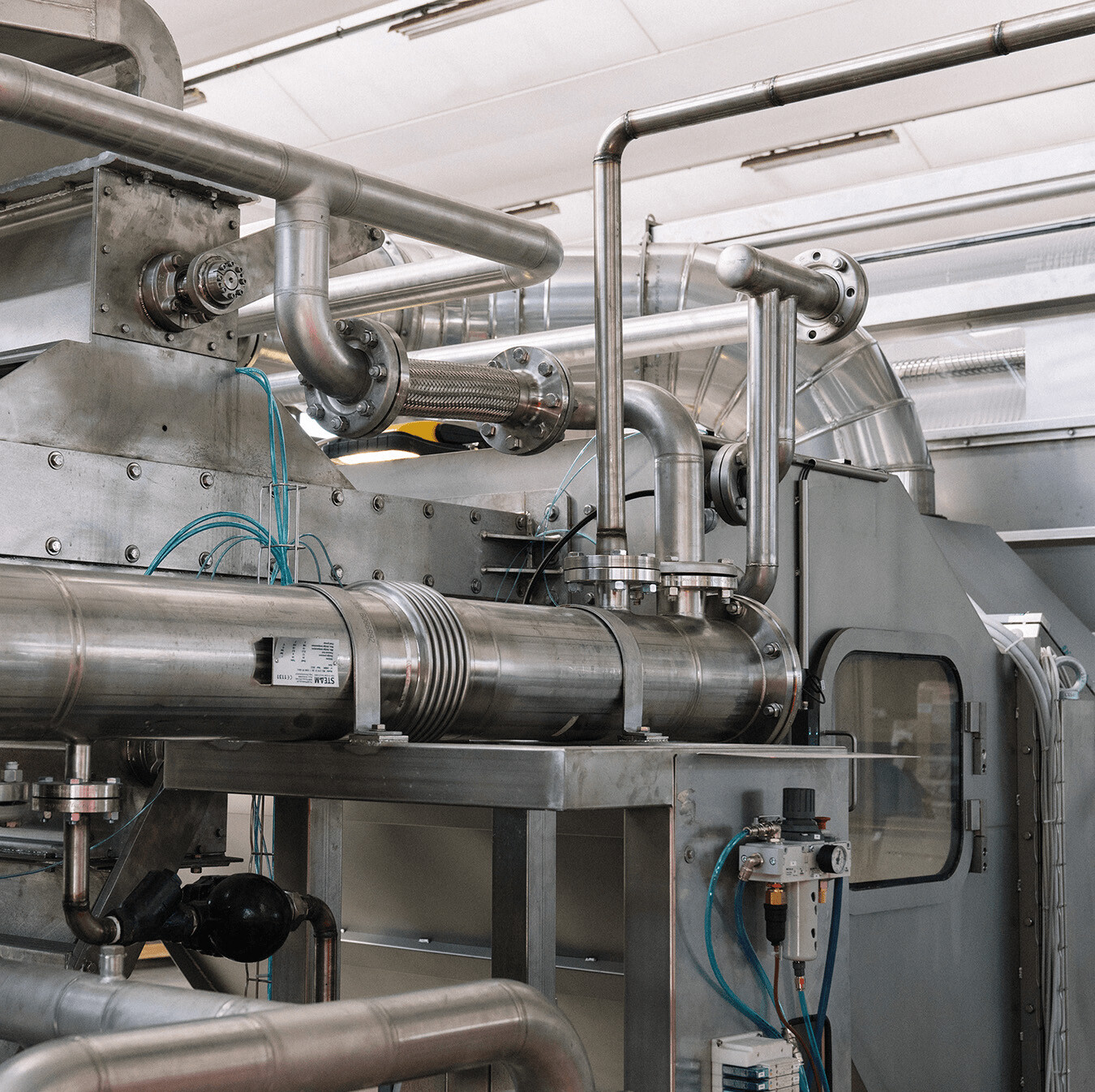
Sensors and process control
Each detail of the process can be controlled with continuity and accuracy, thanks to the availability of several types of sensors and probes. From the level sensors, used to control the water exchange and reintegration, to the temperature probes installed on the recirculation pipes and inside the accumulation chamber of AQUARIA®, to optional sensors such as pH, ORP/Redox, and electrical conductivity.
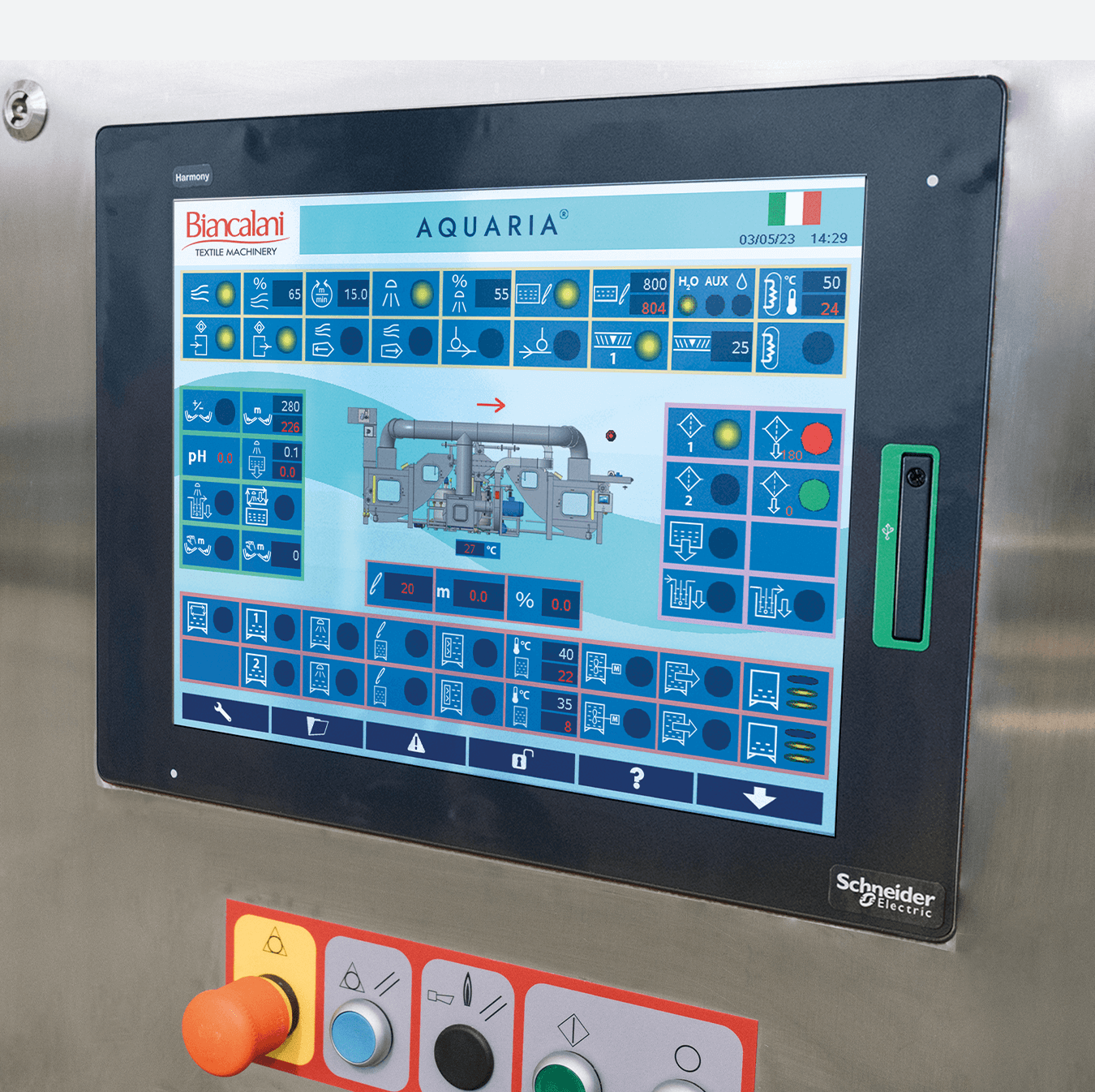
Integrated reporting and diagnostic
Through a user-friendly interface, the touch screens allow for complete control of the whole AQUARIA® line. Recipes, usage statistics and real-time data for each individual module and for the whole line can be visualised and managed either locally or from a remote computer connected to the network. A complete diagnostic system immediately informs the user of possible issues detected at any point of the line, providing complete info in order to facilitate a quick and effective solution. AQUARIA® is also open to directly accessing all the working parameters in order to be interfaced with existing monitoring systems (i.e. industry 5.0).
Download brochure
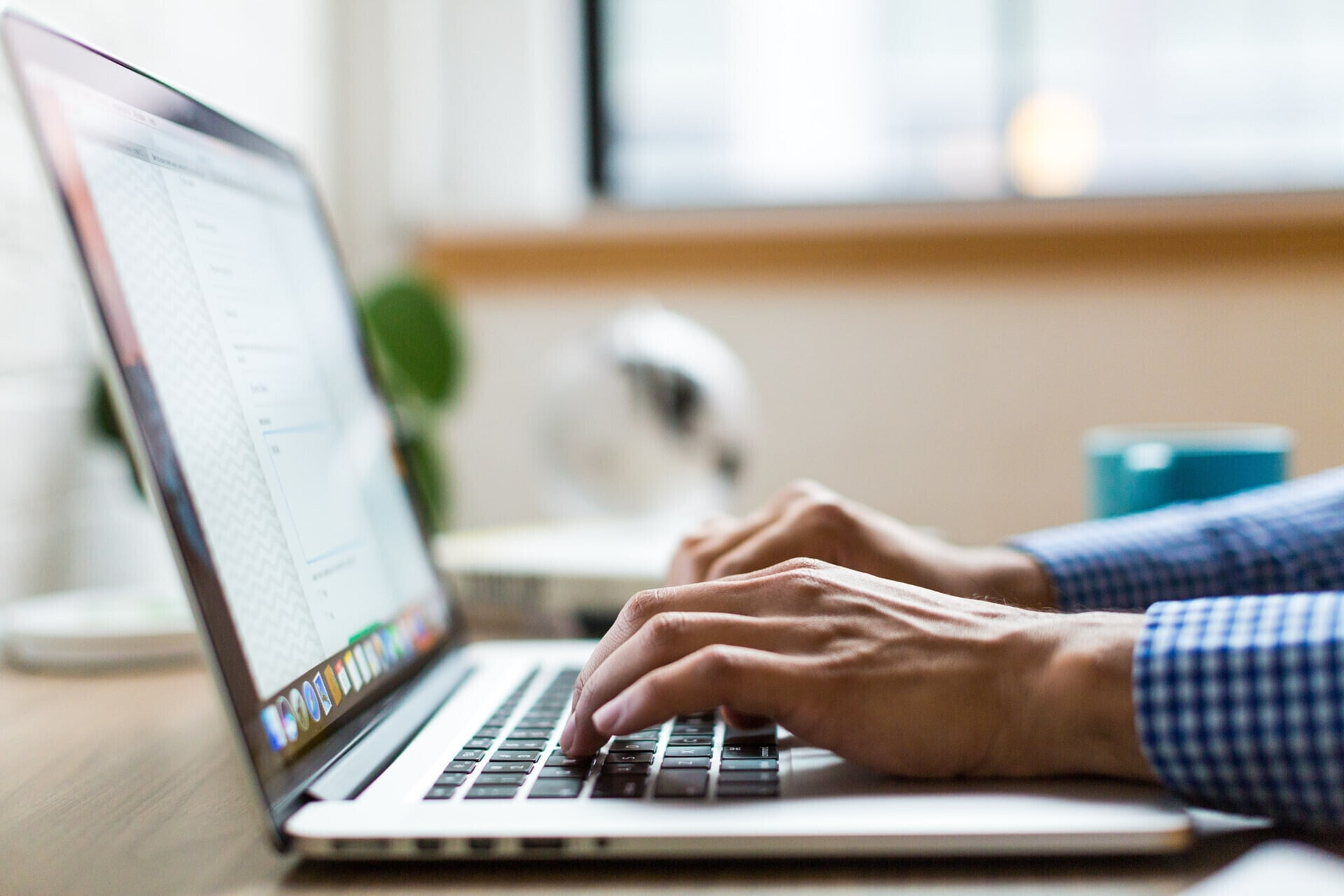
CONTACT & SUPPORT
Write us to get more information or to request a test on your fabrics.
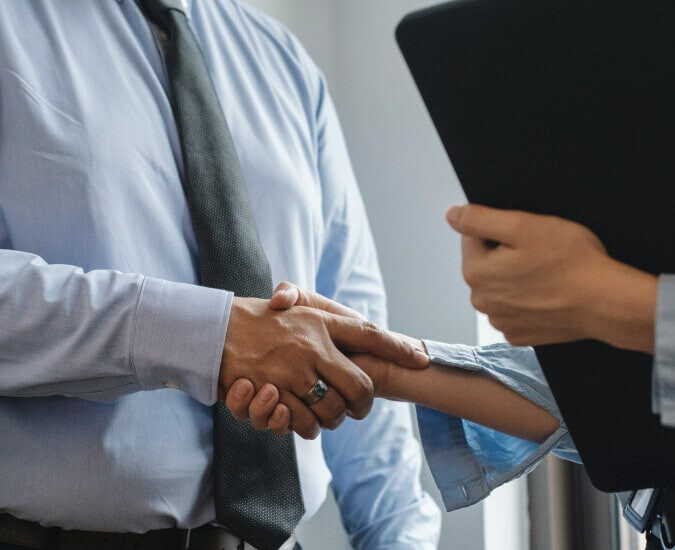
WHY CHOOSE US
At Biancalani we do a lot more for you than just building machines. We listen to your advice and desires and make it easy for you to reach your goals offering you our past as a present: we strive to be part of your future.